top of page
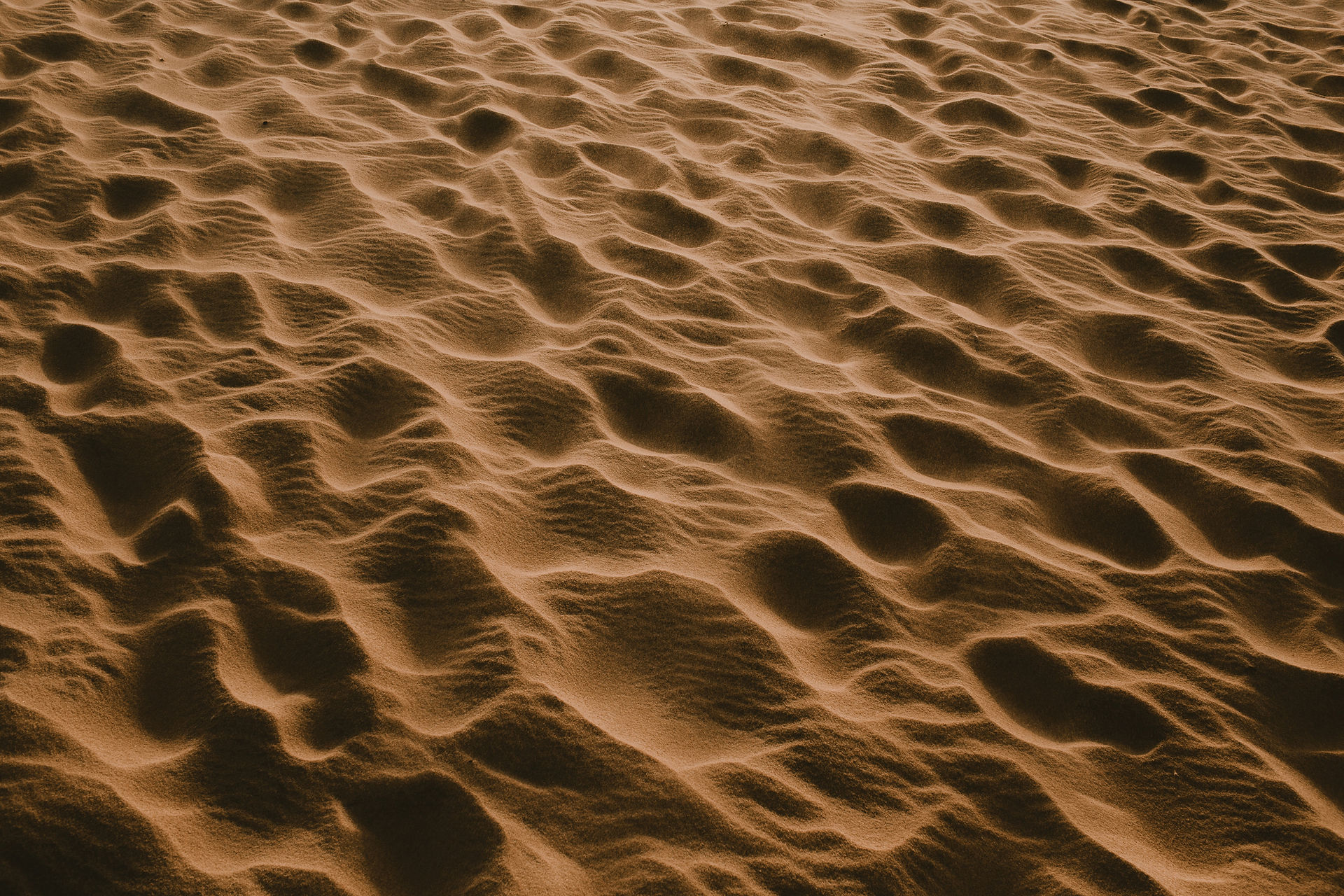
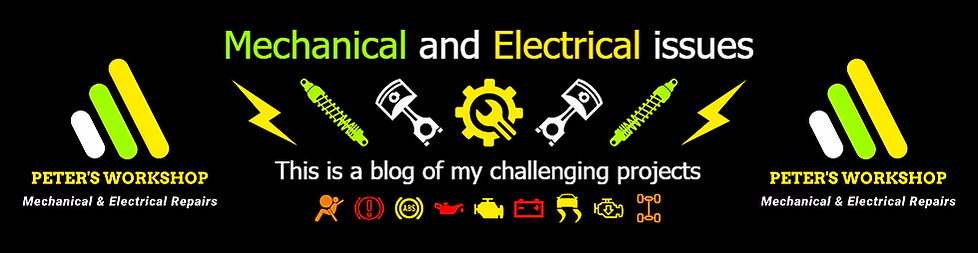
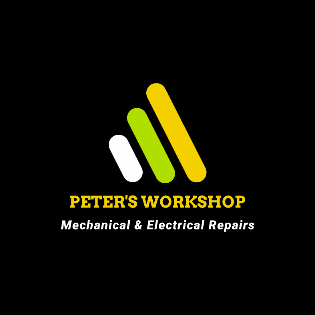
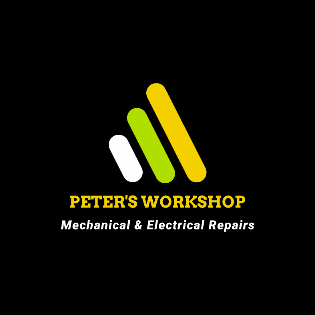
ELECTRICAL
Battery Maintenance
Complexity: Medium
Opening Thoughts
​
I really like dealing with lead-acid batteries, but I can only say with a smile that the battery maintenance was a bit more complicated procedure many decades ago. It is a well-known fact by everyone that nowadays, each lead-dioxide plate can be found in at least one plastic-based or fiberglass bag and has one or more additional different types of microporous protective layers to prevent the soft active mass leaving from the lead grid surface. Thus, the so-called cell short circuit in the traditional sense is no longer a problem.
A few decades ago, this technology was still unknown, and one of the biggest enemies of the accumulators was the mentioned cell short-circuit. In fact, I would say it was basically a natural feature of every lead-acid battery because of the direct contact with highly caustic sulfuric acid and also due to the mechanical resonance and the extreme thermal loads under the hood.
So because of these harmful factors, smaller or larger pieces of lead-containing particles could leave the surface of the soft active mass. Moreover, some gas bubbles may form in the electrolyte during the charging process too, which has an additional slightly abrasive effect as well. As a result of these, the floating particles in the electrolyte formed an electrically conductive deposited sludge layer on any surface.
So long ago these small - mainly lead-containing - particles could be accumulated at the bottom of the battery, which meant finally an electrically conductive sludge mass. In the good old days when there were no separator bags around the plates, this sludge could cause the mentioned cell short-circuit. A sign of this was a sudden drop in voltage level by several Volts due to the short-circuit current, because the voltage between the closed cells dropped suddenly to 0 V. Thus, the voltage measured at the battery terminals was no longer 12V, so the normal 6-cell voltage because two or more cells were already 'merged together'.
So at those times, it was a partial solution for old mechanics to pour out the entire acid content into a proper bowl, and then the battery was washed through very thoroughly with distilled water. The smooth tap water was not good of course because the operation of batteries depends on the sensitive balance of the dissolved salts of sulfuric acid. After that, the old acid was filtered through a fine filter and poured back into the cells, and then could only the charging began. Anyway, the more affluent individuals could mix a completely new electrolyte with a maximum of 30 g/cm3 sulfuric acid content as well. Fortunately, there is no need for this complex procedure nowadays, but I still have a small amount of spare electrolyte if I need it in the future. :)
Nowadays, there are plenty of electric-based tools that can be used to maintain lead-acid batteries, as shown in the image below. By the way, many more devices are missing from that picture, such as my automatic sulfate dissolving electronics and the charge balancing electronics or the electrolyte repair fluids.
I would like to emphasize here that this article is not a doctoral dissertation and I only deal with lead-acid batteries as a simple hobby. I wouldn’t be surprised if a sentence or two needs to be adjusted. So I would be very happy to receive corrective feedbacks too.
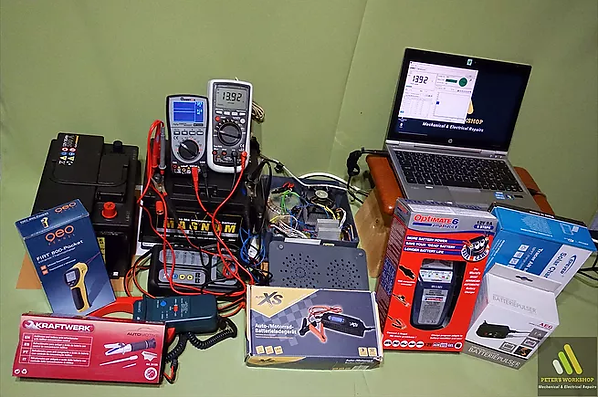
Quality of lead-acid Batteries
​
I would say that the 3 most important quality factors of lead-acid batteries are the amount of stored energy, the rate of self-discharge loss, and last but not least the maximum cycle time.
In addition, the resistance to mechanical resonance and the heat load tolerance is also quite important parameters too, but these factors also appear indirectly in the 3 main factors mentioned above. Moreover from an engineering point of view, each battery has a structural estimated lifetime as well, which must be taken into account because the lifespan of batteries strongly depends among others on their internal corrosion too.
Anyway, the capability of the batteries is very limited by their standard plastic container size. Moreover, that is not surprising to me, but surely many don’t know that the batteries with good starting ability and the well-known long-life batteries are in two completely different groups in terms of lifespan and used materials point of view. In my opinion, these two concepts do not really exist in one product because a compromise has to be made somewhere. However, there are Dual Purpose Batteries on the market as well, which can certainly combine both advantageous properties.
Finally, my last personal thought about another important quality influencing factor. The purity of the lead and various alloying materials used in the manufacture is not the last aspect in terms of quality.
Let's quantify briefly below some electrical properties which can describe a given battery.

Measuring Numbers of lead-acid Batteries
​
The 'nominal quality' of a lead-acid battery can be described quite well by a few metrics.
I think it is definitely worth briefly describing them here.
Nominal voltage (V)
It means theoretically that the no-load voltage of 1 cell is 2 V, and there are 6 individual cells in a conventional lead-acid battery, therefore its nominal voltage is 12 V, but be aware that the nominal voltage is not equal to the idle voltage, because the idle voltage means the voltage measured in a completely unloaded state.
Cold Cranking Amps (EN)
It means the value of the current that the battery can deliver without any problems for 30 seconds at a temperature of -18 °C, meanwhile, its voltage does not drop below 7.2 V. In the case of car batteries, this value typically starts from about 3-400 A.
Capacity (Ah)
I would say this value is used to characterize the charge storage capacity, in other words, it means the energy absorption capacity of the battery.
To be clear, I’ll just quickly comment here, that 1Ah is equal to 1A of current for 1 hour. This unit is derived from the Coulomb signed scalar which means basically: 1 As (Ampere * sec.). To be more precise, the 1 Coulomb (C) means that amount of charge which flows through the conductor in 1 second at a current of 1 Ampere.
Internal resistance (Ohm)
Every battery has some internal resistance, but this value is not known because it is not published by the manufacturers either. The internal resistance of batteries depends mainly on the purity of the used raw materials, on the cell thicknesses and on the density of the electrolyte, which is an electrically conductive fluid.
Don't forget that the thinner the lead plate grids, the lower its internal resistance, and this way the battery can produce much higher starting current. This is the main reason why the volume of batteries did not change, but their starting current has drastically increased in recent years.
In my opinion that could be the main reason why the newer higher capacity batteries fail much faster as earlier, because under high-current load, the thinner lead grid plates may damage due to the huge load shock, but let's not go so far because the picture is more complex than that.

Let's analyze the Electrolyte
​
The electrolyte contains usually about 25-30% highly caustic sulfuric acid and its remaining 75-70% content is simple distilled water. Due to the electric charge of the battery, some additional clean water is also generated inside the cells in both liquid and vapor forms too.
Furthermore, during charging, the dissolution of the increased sulfuric acid concentration in the free water content of the electrolyte results in strong warming as well. Therefore, as a result of water evaporation, since sulfuric acid does not really evaporate, the entire water content of a conventional battery continuously decreases over time, and this is especially the main reason why it sometimes needs to be refilled. Anyway, the pure tap water is out of this question, as the electrochemical processes in the lead-acid battery are based on the dissolved sulfate salt content of the sulfuric acid.
I would like to mention here quickly, that there are already maintenance-free, so-called VRLA (Valve Regulated Lead Acid) batteries as well, where thanks to some additional catalysts and to the more complex valve types, the generated water vapors are converted back to liquid water very effectively for the electrolyte.
Thus, in theoretical calculations and measurements, the density of the electrolyte represents the exact ratio of sulfuric acid to distilled water. The nominal value is used to be between 1.25-1.30 g/cm3. It is possible to measure the acid density with refractometer too - as you can see in the picture below - because I also bought one to be more precise in this field too.
​
So the sulfuric acid density of the battery acid is measured in kg/l or in g/cm3, and the scale of the refractometer can show the following categories:
- RECHARGE: 1.10 - 1.20 g/cm3,
- FAIR: 1.20 - 1.25 g/cm3,
- GOOD: 1.25 - 1.30 g/cm3.
​
So due to the electrochemical processes, when the battery is discharged, the density of the sulfuric acid decreases. Furthermore, if the density of the electrolyte decreases, the capacity of the battery will be also decreased. Moreover, it is a well-known fact from high school, that sulfuric acid contains mainly sulfate salts, which will be deposited on the lead plates during the discharge process, and these crystalized sulfate salts will be dissolved back when the battery is charged, as I referred to this process above as well.
For this reason, as I mentioned earlier, never fill the battery with clean tap water for maintenance, due to the sensitive sulfate salt balance of the electrolyte because there are additional, unnecessary dissolved salts in the tap water, which could deposit as a harmful and corrosive layer on the lead plates too.
Furthermore, everyone knows already that sulfuric acid contains mainly sulfate salts, which can be dissolved in water very easily. So when the sulfuric acid density of a discharged lead-acid battery decreases, then its freezing point will be also decreased, because the sulfuric acid content of the electrolyte is converted to simple water and crystallized sulfate salts.
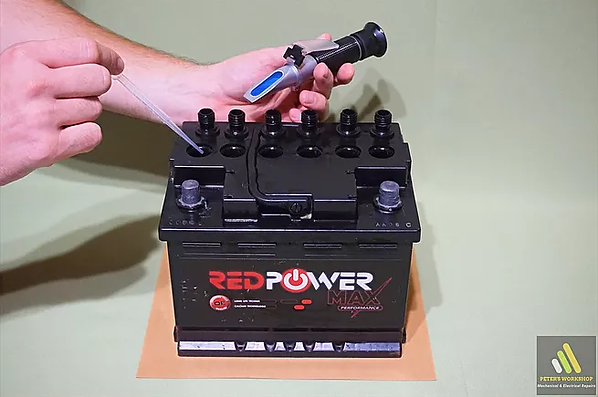
I think it is well known to everyone that there are batteries on the market with a built-in acid density meter too. For these types of batteries, the density is simply indicated by a green ball, which is floating in the acid, according to the density level of the electrolyte. If the density is high, the ball floats on the surface of the acid and this time we can see a nice green dot in the transparent window on the top of the battery. If the battery is discharged the acid density is lower, thus the buoyancy force acting on the ball is less, so the ball sinks to the bottom of the container, and in this case, we only see a black mark on the window. As you can see in the picture, my demonstration battery is already discharged (12.45 V, 250 EN), and it also has a window in the middle of the top cover but shows a completely black mark.

Why does the voltage level decrease under load and why does it rise again after the load?
​The graph below shows this question very nicely, but I'm sure everyone has experienced that the starter engine speed constantly slows down if the internal combustion engine won't start. The short explanation is that under load, the density of sulfuric acid in the electrolyte decreases directly in the area of ​​the plates, thus only a limited amount of sulfuric acid is in direct contact with the lead plates and the conductivity of the electrolyte will be also reduced. Therefore, it is worth waiting 1-2 minutes before the next ignition attempt, because due to the slow diffusion process, during this time the sulfuric acid concentration will be normalized on the active surface of the lead plates.

Perhaps that would be also interesting to mention, that after the charging process, the voltage level decreases for similar reasons, because after stopping the internal combustion engine, the generator no longer charges the battery, and the voltage level drops back pretty slowly.
Starting from the things mentioned above, as a result of the electric charge, the sulfuric acid is formed from the sulfate salts deposited on the plates, thereby the concentration of the sulfuric acid will be increased near the surface of the lead plates. Thus, the sulfuric acid appears in higher concentrations in the electrolyte, than further away from the lead grids, and this extra amount of sulfuric acid will be mixed in the electrolyte after a short time, so as a result of this the voltage level slowly sinks back, as shown in the picture below.

Deposited harmful lead sulfate layer on the Electrodes
​
I have also wrote in the 'Opinions and Thoughts' section, that:
Pb + PbO2 + 2H2SO4 <=> 2PbSO4 + 2H2O (+ 2e-)
[lead + lead-dioxide + sulfuric acid <=> lead sulfate + water (+ electrons)]
During my high school years I had already learned from chemistry lessons that this formula explains us briefly, when the battery is discharged, the electrolyte continously loses its sulfuric acid content. As a result of this a crystallized primary lead sulfate salt layer is generated on the surface of the lead grids, which is easily dissolvable in sulfuric acid electrolyte.
Meanwhile this process, some water is generated and further 2 electrons are released which can finally ensure the flow of the electric charge. The generated water will be mixed as a liquid in the electrolyte by the diffusion effect and as a result of this the sulfuric acid density will decrease in the electrolyte.
When we are charging the battery, this process is, of course, reversed.
Due to the influence of electric charge the mentioned crystallized primary lead sulfate salt layer on the surface of the lead grids will dissolve back into the electrolyte as sulfuric acid again, but the distilled water content will simply evaporate and as a result of this the density of the electrolyte will increase. This is the reason why need to be refilled the battery cells only with distilled water from time to time.
Don't forget that we never pour sulfuric acid into the cells because the sulfuric acid cannot evaporate so much. On the other hand, a sulfuric acid content of more than 30% would corrode the lead grids and destroy the battery.
BUT, let’s continue this with another interesting process:
Due to the maintenance of lead-acid batteries I think it is important to write here a few sentences about the petrified secondary lead sulfate crystal layer, which can seriously damage the forgotten and unused batteries.
So a lead-acid battery can be completely sulfated with the secondary lead sulfate crystal layer that has been discharged for a long time and has not been charged at all during this long period.
In this case the density of the electrolyte is significantly decreased as described above and thick petrified secondary lead sulfate crystal layer will be built on the entire surface of the plate grids, which means at the same time a strong insulating layer too.
Unfortunately this thick covering crystal layer is no longer able to dissolve in the usual electrochemical way because, as I mentioned, it is an insulating layer from electrical point of view. So if the battery is full of secondary lead sulfate crystals, then no electrochemical processes take place any more and the capacity of the battery will be drastically reduced.
Over the years I have tried many different things to break this layer and I have nice partial results, but it is very difficult to achieve a 100% long lasting solution. In the picture below I would like to show what the petrified secondary lead sulfate crystal layer on the lead grids looks like in the real life.
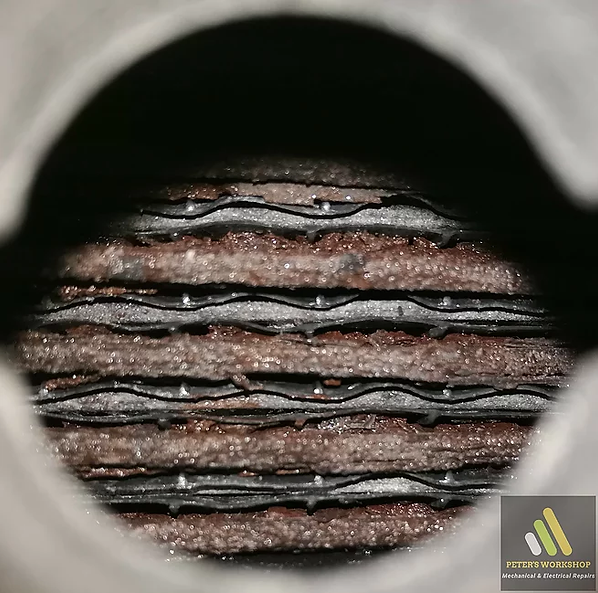
Battery recovery - the big Challenge
​
If the vehicle is in use, its battery is constantly charged. This could be the best circumstance for all batteries, but thanks mainly to the immobilizer and other monitoring circuits, those lead-acid batteries which are left alone in a vehicle for a long time will be (even completely) discharged with low current and in addition, each battery has a natural self-discharge too.
Especially in this case begins the formation of thicker lead sulfate crystals as described above.
There are some tricky solutions for sulfate dissolution with different efficiencies. So the electrical reset is possible with certain pulsating charging signals which takes an extremely long time compared to normal battery charging.
That’s why I said it’s always worth paying attention to our batteries, recharging them a little every few months when they are out of use because this way we can avoid the unexpected inconveniences later. The picture below shows a battery that has been left alone in a vehicle for more than ten years. The sulfuric acid can not evaporate as fast as water, but left a nice white powder on top of the battery, in addition, it brought a small brownish lead oxide mass from inside too.
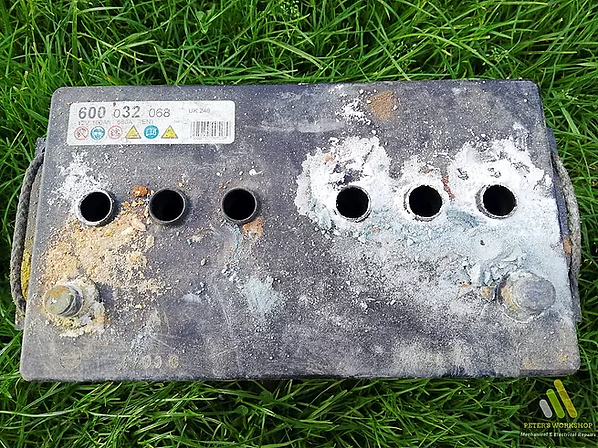
Moreover increased attention should be paid to the temperature monitoring during recovery charging process as well because too much heat may be generated and congested near the positive pole. Especially if the recovery process is started from a deep discharge state, i.e. from a very low voltage level, such as 2 V. I would say it is not worth charging the battery above 45 °C, which value is measured on the side wall of the battery. So the maintenance requires slightly more supervision this time, as shown in the picture below.

If the temperature factor has already come up in this section let me note that lead-acid batteries don't really like the summer heat because they can get an extreme heat shock under the hood next to the internal combustion engine as can be seen in the picture below.
The thermal load is not advantageous for either the electrolyte or the charging process, which also results additional heat generation, since the mixing of freshly produced sulfuric acid means also a heat-generating exothermic process. Moreover in such extreme conditions, loading the battery with high current may break the internal contents.
Otherwise, the water content of a deeply discharged battery is higher because the density of sulfuric acid is lower, in this case, the risk of frost can be a problem more likely. Therefore, it is advisable to check the density of sulfuric acid before winter, which should be optimally around 1.25-130 g/cm3.
To close this temperature topic with a positive thought let me say that, in terms of technical characteristics of batteries, the good news is that the charging current consumption of newer calcium alloy types shows a decreasing tendency at increasing temperatures. Unfortunately, the charging current consumption of the older antimony alloy batteries show an increasing tendency at increasing temperatures which increases the rate of water decomposition at the same time.

Let's turn back to the sulfate dissolution after this important remark.
​The simplest sulfate dissolving devices usually work with pulsating high-voltage spikes. I tried out these too, but I would say that they didn't bring me any breakthrough success. I have already achieved more success with much more complicated microprocessor-controlled devices, which are operating with special current pulse sequences, but these are quite expensive for the average user. I would say that for the long-term success, it is really worth desulfating the batteries once or twice a year with these tools, if we want to keep the full capacity and high cold start capability of the lead-acid battery. Anyway, I usually do this regeneration process especially before winter. Meanwhile this process it is always worth tracking at least the voltage level, to make sure that water decomposition is avoided.
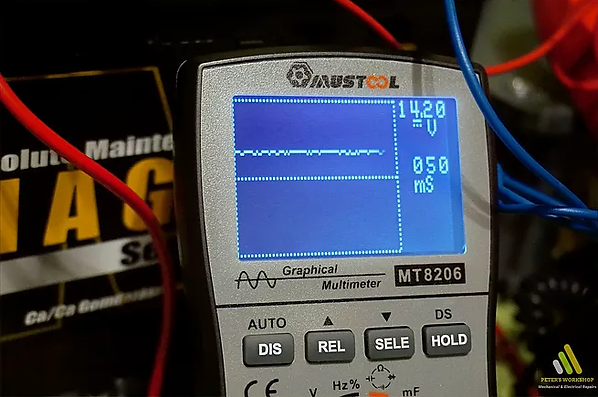
I can say that I like dealing with electronics because I built some kinds of battery maintenance tools too. The central element of the battery charger I designed and built is a 200 VA toroidal transformer. I made the circuit boards also at home using laser printing technology. I designed a two decimal places accurate integrated digital LED display voltmeter into the box too.
This device works in current generator operation mode, where the charging current is self-regulated. Anyway the most important requirement for chargers is to keep the battery voltage level below the 14.4V water decomposition limit, which can be tracked and adjusted easily by a comparator based voltage monitoring circuit too. Furthermore, when the battery is fully charged, the charging current must be continuously reduced, so it must have a nice downward curving characteristic too.
Anyway, calculating the battery charge is not complicated because if we continuously charge a 50 Ah battery with a constant 2 A for 1 hours, we can say that we have already recharged 2 Ah.

Maintenance-free lead-acid Batteries
​
In summary, what is the difference between the maintainable and maintenance-free concepts?
I think this is a point of view issue, because the real question would be that to whom and what the maintenance means.
It is true that the self-discharge loss of maintenance-free lead-acid batteries is relative minimal, therefore they can be stored for 1-1.5 year, but for me, every battery requires some kind of maintenance at least every six months, especially when the battery is out of use. So briefly, it is worth to maintain periodically the maintenance-free lead-acid batteries as well with appropriate charging pulses, as I described above.
By the way according to the official source, the lead acid battery is considered to be maintenance-free if, during laboratory tests (at 40 ° C ± 2 ° C for 500 hours at a constant voltage of 14.4 V ± 0.05 V (2.4 V / cell)) for 1 ampere hour (Ah) water loss the water consumption does not exceed the 3 grams.
Many new and excellent technologies already exist in this field too. The manufacturers have achieved incredibly beautiful results with various useful catalyst additives and alloy materials and with different advantageous designs of gas space, because the vapors - generated during the electrochemical reaction - must be converted back into liquid water.
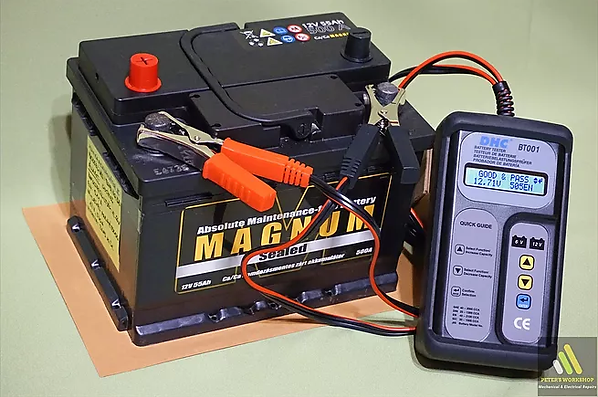
Non-maintenance-free Batteries
​
Unfortunately, the distilled water cannot be filled into the battery without the 6 caps on the battery cover. However that is quite harmful, when the top of the plates are visible from the electrolyte, because the reaction is limited only to the part which is floating in the acid bath. Thus, the high current load will result a very unequal load over the entire surface of the lead plate grids. Furthermore, when the low water content of the electrolyte is not compensated, the density of sulfuric acid will be increased, which means a higher corrosive effect to the plates.
By the way, in many cases, these caps are there, but they are only glued off with a nice marketing sticker. In my personal opinion it can - a bit incorrectly - refer to a completely maintenance-free battery. Anyway, if someone breaks this sticker, the warranty will be lost.
As you can see above, I like to check the electrolyte level together with acid density, and I also like to make sure the battery is charged properly. So, before starting the charging process for non-sealed batteries, the acid level must be always adjusted with deionized water, if necessary.
​​​
If there is no level indicator, I used to set the appropriate acid level with small strips of papers, which were cut out of a square grid maths exercise book. On these small strips, I can mark easily 12 to 13 millimeters, measured from the bottom end. Then I unscrew the actual cell cap and I dip it in the acid until it reaches the top edge of the lead plates. If the acid level is low, I pour some deionized water into the liquid to increase the electrolyte level back to 12-13 mm. Too much liquid is also harmful because it reduces the expansion space of the vapors.
Finally, the traditional antimony-alloy batteries (PbSb) always require much more care than their other calcium-containing counterparts. There is a simple explanation for this. Due to the highly corrosive effect of sulfuric acid, the antimony particles are able to dissolve in the electrolyte. Thus, the generated positive antimony (Sb+) ions - because of their opposite charge - can easily form a disadvantageous deposit on the surface of the negative electrodes. This is a less harmful process at first, but later increases the decomposition of water, because the electrical energy intended to charge the battery will not be absorbed into the electrochemical recombination, but begins to decompose the water content of the electrolyte.
In summary, the larger the battery - as shown in the image below (12V, 180Ah, 1000A) - the more attention should I pay to its maintenance to avoid the unnecessary expenses in the future.

Thank You for reading this article!
bottom of page