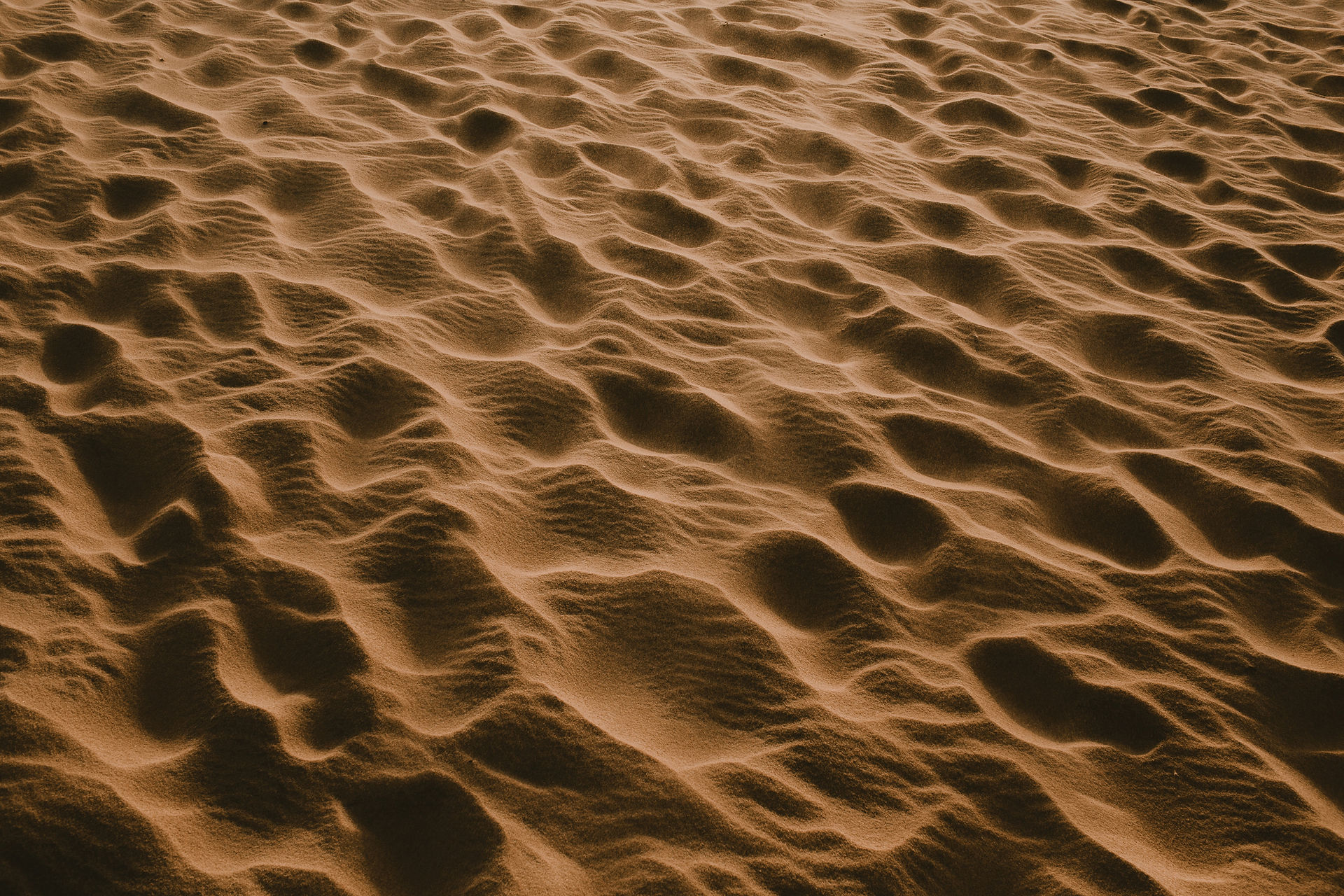
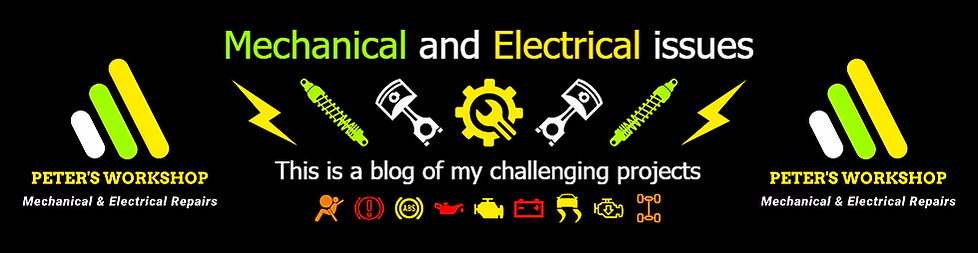
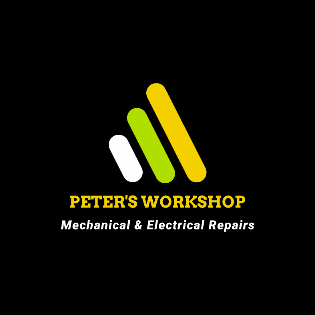
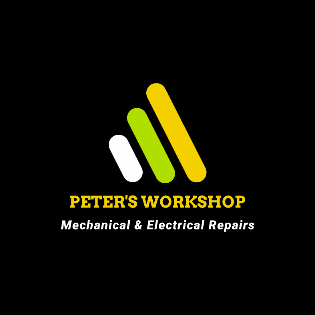
MECHANICAL
Projects










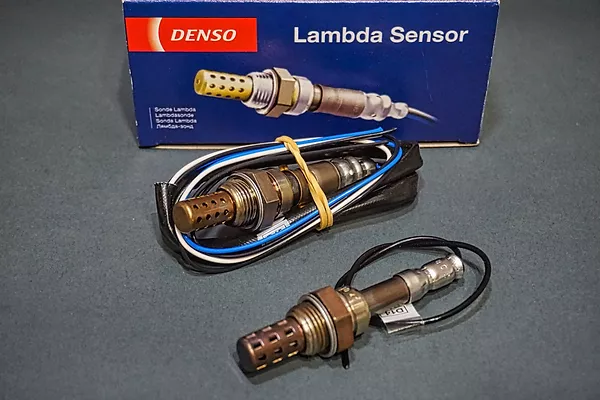


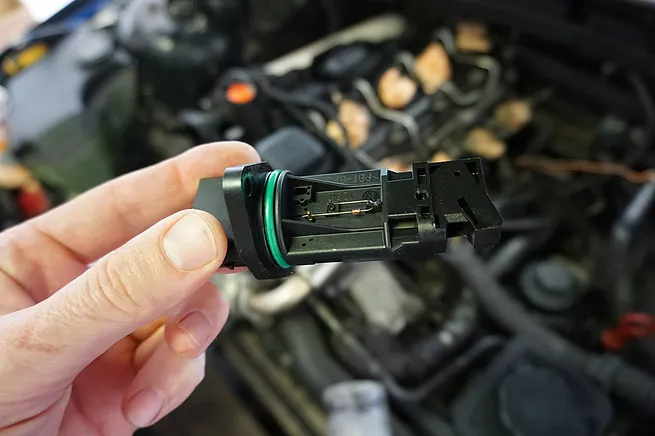
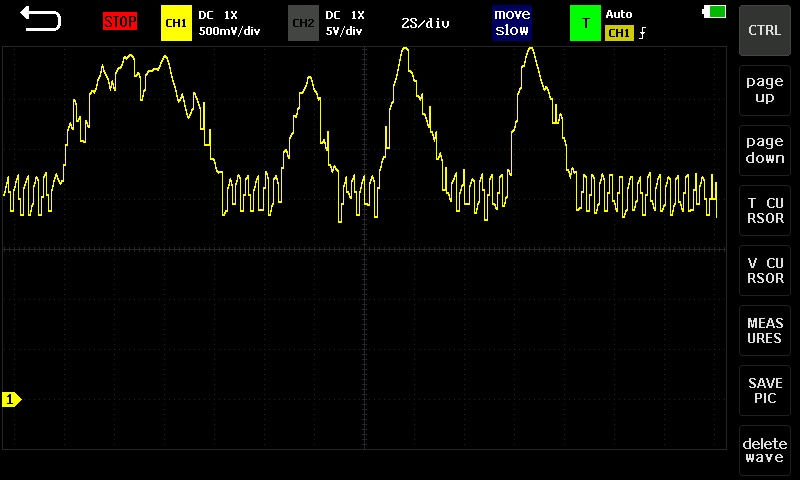


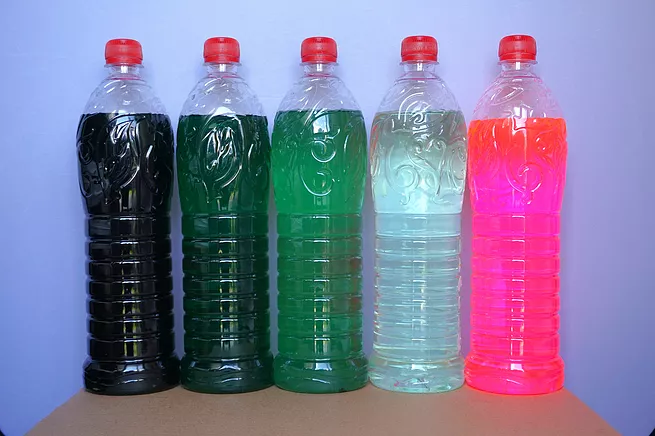


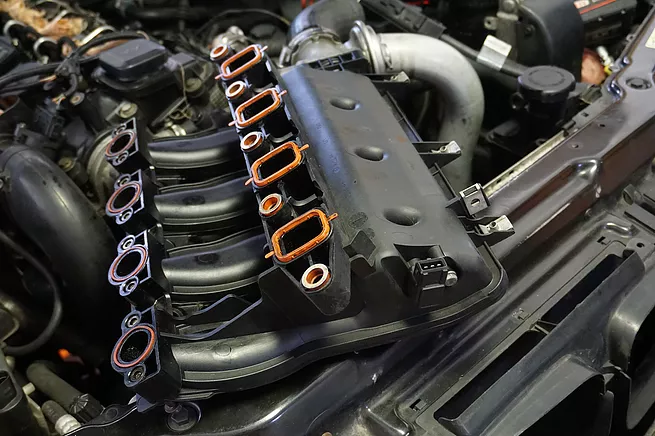

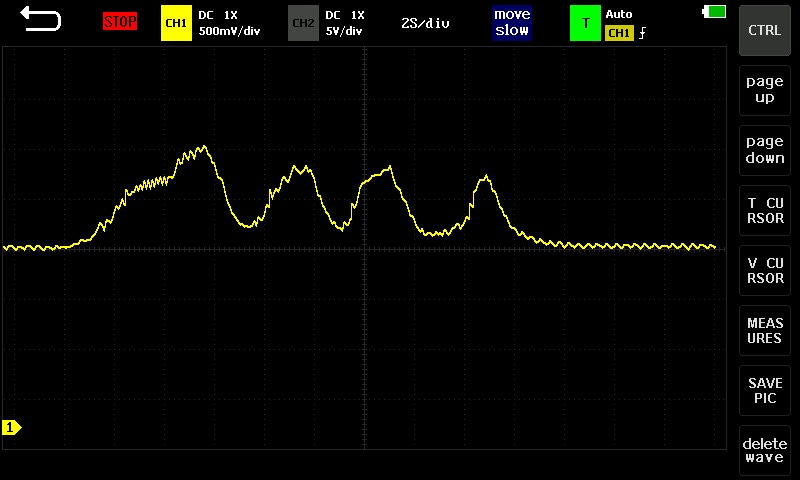
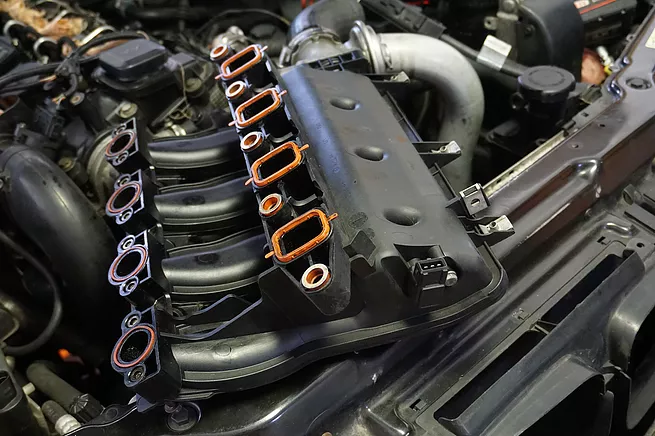




Ongoing Topics
TPS sensor
Knock sensor
CMP sensor
EGR valve
Fuel injectors

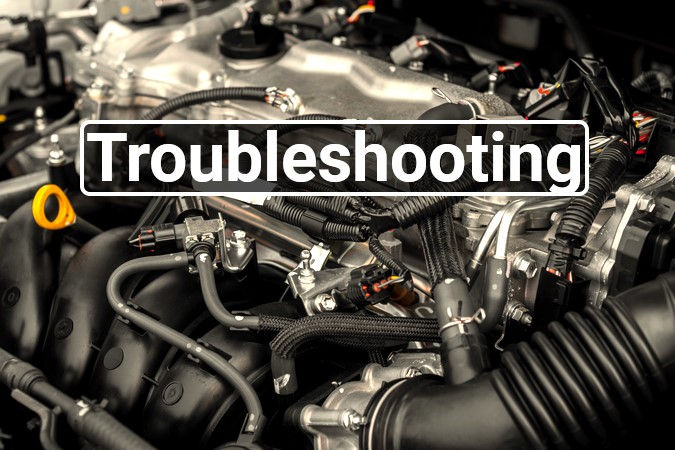
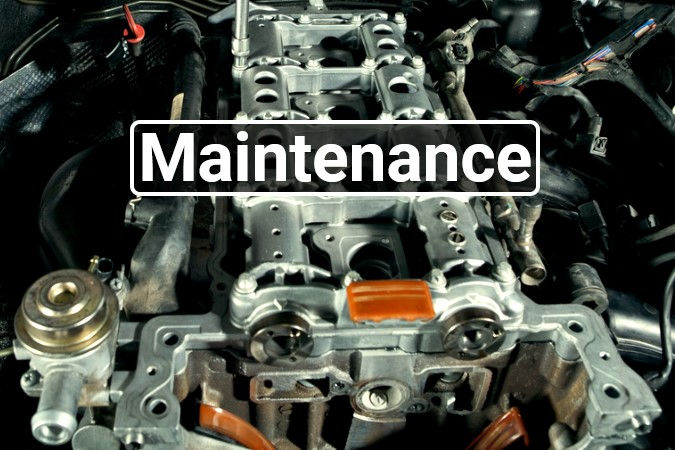

Safety first!
Never take unnecessary risks!
Do not try experiments at home!
Call an expert if you are not qualified!
A few words about this topic group
​
The purpose of these articles is to illustrate my technical approach and personal opinion about the mechanical challenges I faced so far. To tell the truth, this is not a super easy challenge because I have to compile valuable content in a third language, but despite this fact, I want to achieve a dynamically increasing level of quality to make this site a good investment for readers in terms of time. Please always keep in mind this is just a blog site that presents solutions exclusively to my own issues. Its main goal is entertainment and nothing more.
For me, the joy of the creation process is one of the most important factors in these projects. I love exploring new technical areas that are useful and increase my field of vision. I'm able to immerse myself in all kinds of challenges and almost no matter what technology or device it is. Perhaps at first glance, some projects may seem playfully simple and almost weightless in terms of difficulty, but even these repairs can offer many interesting surprises even for an experienced mechanic.
In my opinion, all sorts of mechanical repairs should always be carried out precisely and patiently. Don't forget that it is not allowed to repair mechanical and electrical devices without appropriate qualifications. For me, in connection with mechanical maintenances, one of the most important aspects is that mandatory - even official - technical inspection is required after each successful repair process.
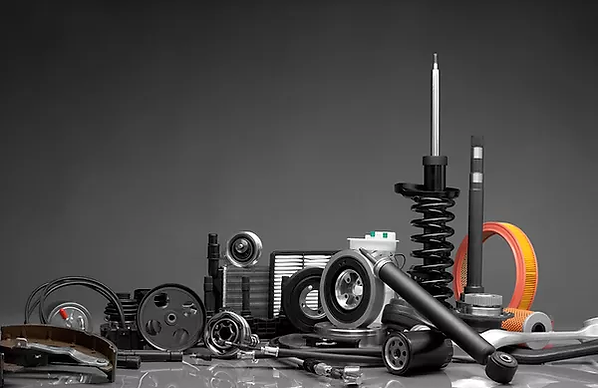
I usually focus on the very tiny details, maybe that’s my main specialty, and I know for sure that it’s not worth underestimating even simple maintenances if we want a perfect result, especially in the long run. Indeed, in the case of minor repairs, beyond the time demand and experience, other non-negligible factors should also be taken into account. It is enough to think only about the right set of special tools, which requires serious investment, and not to mention the necessary technical specifications, which entry conditions are missing almost by default for most DIY mechanics. Major mechanical repairs are already complex processes, where it’s worth thinking several steps ahead and sometimes applying amazing tricks, which I have also learned from earlier experiences or other mechanics.
So it is worth cultivating more than just a particular topic since the complex connections between professional fields must also be seen from a slightly more distant perspective. That's why I think that the wisest attitude is to be open to other technical areas because it greatly increases individual problem-solving skills.

Gaining more and more Experience
​
This is actually the key process that can only be started and should never get stuck at any level.
It is worth keeping in mind that there is always room for improvement.
At the beginning of this learning process, my vehicles gave me the most of the inspiration for repairs and assemblies in such a way that they seldom had any problems, but despite this fact, I disassembled them regularly. I did a lot of preventive interventions on them just to unscrew and analyze them at even deeper levels.
Thus, step by step, I gained more and more practical experience and was able to further improve my theoretical knowledge effectively. As a result of these activities, my vehicles were considered almost like reference units at the vehicle inspection stations. Then gradually, I dealt with even more complex challenges and with other vehicles over time, and this way I got more and more into the sophisticated details.

I put a lot of resources and time into self-improvement and of course, I bought myself wrenches and special tools for the workshop rather than anything else. I think if someone likes this kind of process that makes something better, there’s no need to explain it further.
If equipment has already been mentioned, I think the golden rule - which can save many brain cells - is familiar to anyone who repairs more often, so it is always worth working only with high-quality tools. I grew out of the wooden handle screwdriver and hammer pretty quickly as I realized that I needed to build a special tool park first to get better results. The last one is the time factor, which I would like to emphasize separately. I think the saying that good work takes time is very true. After all, a calm and analytical attitude is beneficial, especially for non-routine tasks, from which the most experience can be gathered.

Reliability + Durability = Quality
​
I think so, only these 3 factors together can define an uppercase Brand for any technical product.
The mentioned factors are freely interchangeable, but the main concept will always be the same.
Other less interesting features, like trendy design and universal multifunctionality, are usually only important for a good marketing strategy.
What is reliable and durable is usually the best solution for any technical purpose, even if not the most beautiful. During my work, I keep this pretty important rule in mind, whether it’s simple maintenance or designing a completely new device. So I chose this formula because it reflects my main philosophy on technical issues in the most concentrated way.
I feel like the market is hungry for high quality in every field. Despite the seemingly large selection, it is often difficult to buy devices that meet the desired minimum expectations. That’s why I prefer even 20-30 years old reliable and durable techniques whose greatest virtue is noble simplicity and quality. Even the complete overhaul of these machines is often not a particular challenge, not to mention the rapid cost recovery.

Focusing on details but thinking in the system
​
Let's not forget that the perfect solution always strives for simplicity and balance. It’s not enough to focus only on the faulty component itself, but it is essential to look through the whole system while finding the solution to a specific issue.
Let me give you a perfect example of this. Let's take a single-cylinder gasoline engine where the oil pressure indicator system is missing. In addition, the material of the oil and water pump gear is also plastic in this internal combustion engine, which is in itself a weak solution compared to metal. The first thought would be that such a weakened component may be part of planned obsolescence, or the costs savings may have been the final goal.
My very first thought was to eliminate this potential cause of damage locally and quickly replace this part with stronger metal gears because if something gets stuck at the oil pump, the plastic gear will break easily. If the engine lubrication stops, it can cause insanely serious damage to the engine very quickly because, as I mentioned above, there is no oil pressure indicator either.

Let's go deeper into this question. It's all true, but in terms of the global approach, there are also safety reasons in the background from the entire system point of view. If the oil pump got stuck, the much stronger metal gear would further force the drive, which could lead to other serious damages, where not only a cheap plastic gear would have to be replaced. This would obviously be a much worse scenario. So the Japanese engineers did not accidentally weaken these plastic gears, as their purpose may have been to indirectly protect the entire system.
I think it makes more sense to install an additional pressure sensor - at the appropriate point on the engine block - with an indicator light on the instrument panel to make sure the oil pump is working properly. If the oil pressure would suddenly disappear, we could see it immediately and stop the engine in time to avoid further damages. Thus, this bridging solution would strengthen the system globally with the least compromise.

To make this example even more complete, let me say a few short sentences in advance about the technical implementation that I imagined for this project. I quickly found a suitable oil pressure measuring point on the bottom of the engine block, but its original screw thread was 12 x 1.25 mm, and the idle oil pressure at this point was only around 0.5 bar.
So, I was looking for an engine oil pressure sensor with a switching limit of 0.3 bar because it will certainly not give a false signal during operation. In addition, the maximum possible wrench size for the prospective oil sensor should not exceed 19 mm, due to the lack of space because I will have to be able to tighten it a bit with the 19 mm fork wrench.
Of course, with such restrictions, there was no engine oil pressure sensor on the market at all. Browsing through several catalogs, I found only such an available sensor - with the mentioned 0.3 bar switching limit - which had only a too small 10 x 1 mm screw thread, but on top of that, it had a large 22 mm fork wrench size. In light of all this, the difficulty level of this challenge was pretty high, but I also found a bridging solution to it.
The selected sensor got a 10 x 1 / 12 x 1.25 mm beautiful copper bushing, and its wrench size had to be converted back to the desired 19mm very finely with the help of a metal lathe machine.
So from now on, we only need a nice red indicator light and a few meters of wire - as shown in the picture above - and the necessary preparation steps for this project are pretty much ready.
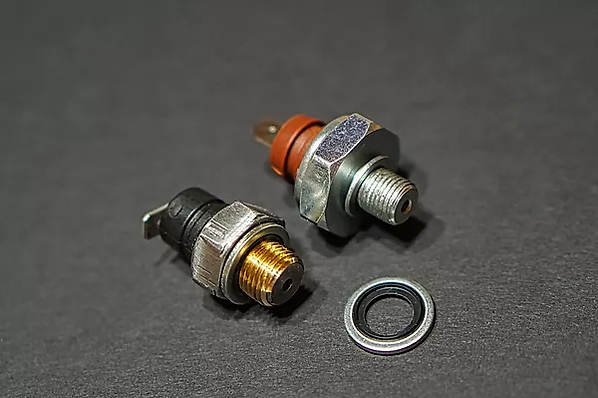
Keep in mind, before you want to do something useful, that it is forbidden to take even the slightest risks in safety issues, and always take precautionary steps to protect yourself!
Wear protective glasses and gloves, but not only when necessary, because it would be best if it became a habit in the workshop!
