top of page
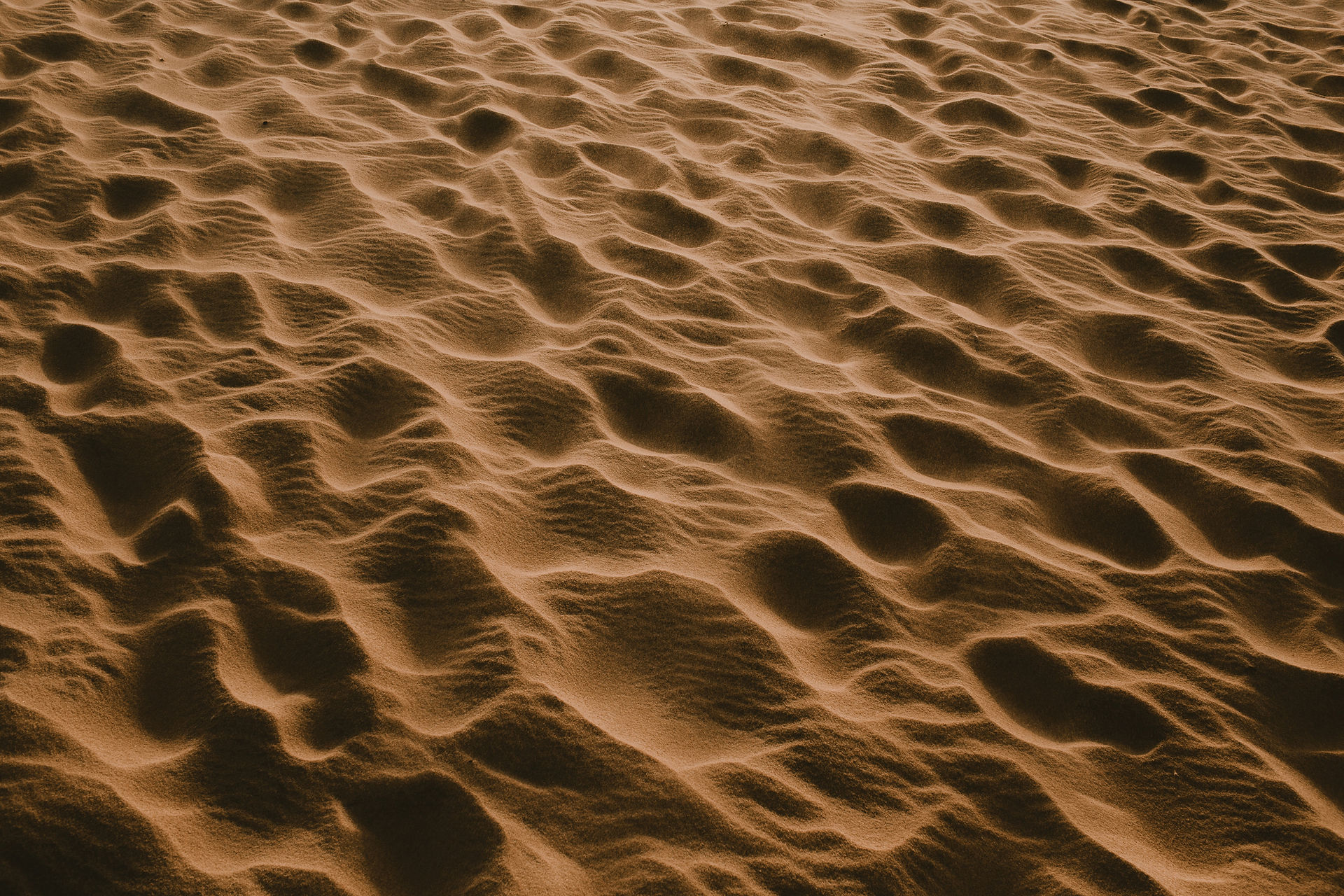
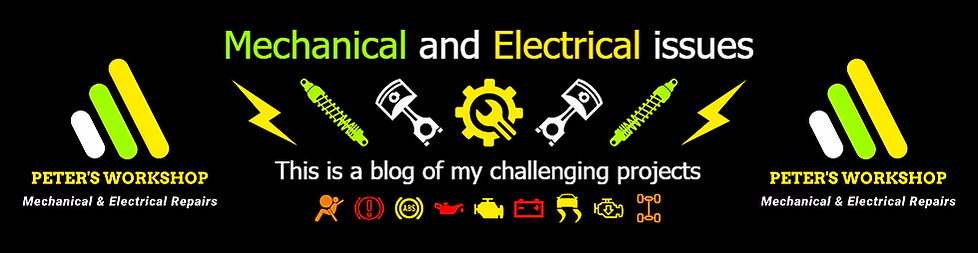
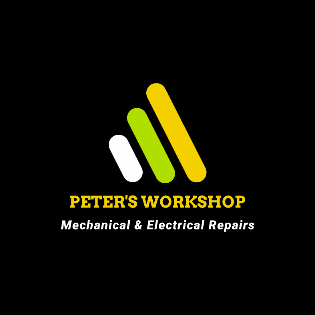
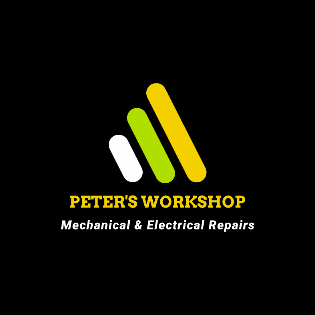
MECHANICAL
Lambda sensor
Zirconium dioxide type Oxygen sensor
I'm quite sure that it is one of the best known and most mentioned sensors in vehicles, even if its construction and operation are not so well known to many hobby specialists. However I think so, it’s worth being aware of its basic properties because it’s not a very cheap sensor type, and in addition to this, there can usually be more than one in most vehicles. Moreover, I'm sure that too that in several cases they are replaced quite unnecessarily since it is more likely, that this sensor generates probably the most and most common DTCs in vehicles older than ten years or driven more than 150-200 thousand kilometers. In my opinion, these are especially true because this sensor is actually located at the end of the entire chain and indirectly monitors the quality of operation of the internal combustion engines.
In terms of its main tasks, the lambda sensor - also known as oxygen sensor - has to monitor basically the amount of unburnt oxygen content in the exhaust gases in accordance with the emission regulations.​
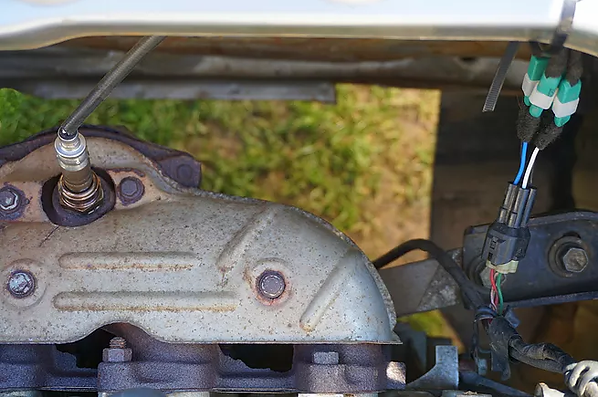
From the technical point of view, there are at least two oxygen sensors - two per cylinders row - in the exhaust system. The first oxygen sensor must be mounted usually in front of the catalytic converter - in the exhaust manifold - for continuous monitoring of the unburnt oxygen content of the exhaust gases, but the second oxygen sensor is located in front of the rear muffler.
Further refining the responsibilities it is very important to know that only the output signal of the first oxygen sensor - it works in a much warmer environment by default - is required to calculate the appropriate air-fuel mixture ratio, and the rear oxygen sensor has to monitor the efficiency of the catalytic converter.

It is worth emphasizing that oxygen sensors require high temperatures - they can only work properly above 300 ° C - for optimal operation. Therefore, they often have at least one but not more than two separate electric internal preheater circuit to send the appropriate output signals as soon as possible to the Powertrain Control Module, for that reason, because the PCM module has to calculate and set the optimal air-fuel mixture ratio and ignition timing for the engine. In terms of their wiring the single-wire and two-wire oxygen sensors, of course, have only one signal wire, and the three- and four-wire oxygen sensors have one or two internal preheater circuits too.

The Lambda Factor
The lambda factor itself is only the ratio between the amount of the intake air and the amount of air required for optimal combustion.
I don't think it's hard to remember that in ideal conditions, 14.7 kg of intake air is required to burn 1 kg of gasoline - and 14.5 kg of air is required to burn 1 kg of diesel - in the case of an internal combustion engine.
If the amount of intake air is less than the amount of air required, the air-fuel mixture will be too rich in fuel and the lambda factor will be less than 1. This situation can be caused, for example, by a clogged air filter, or the MAF or MAP sensor has just become dirty and therefore detects too little intake air, but it is also worth checking the throttle valve as well because the amount of deposit in the throttle body housing can be too high and it can already affect the position of the butterfly valve, or even the butterfly valve is in mechanical trouble, but it can also be affected by the intake air temperature and the engine coolant temperature too.
In this case, the fuel consumption will be high and the engine will smoke even under light load, and in addition, it will run quite unbalanced.
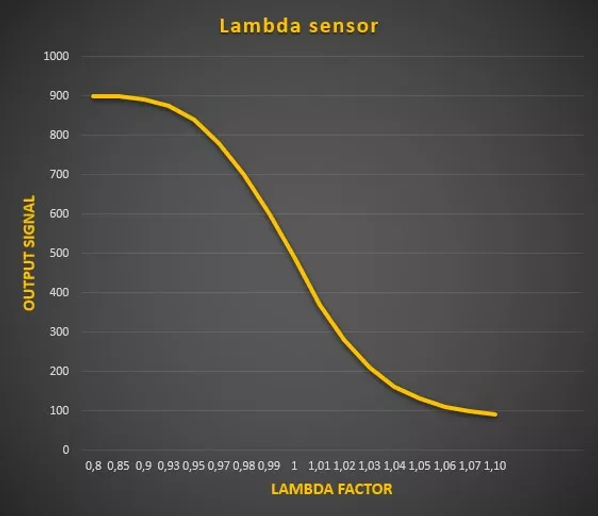
In the opposite case, if the amount of intake air exceeds the amount of air required, the air-fuel mixture will be too weak in fuel and the lambda factor will be greater than 1. This situation may be due to the low amount of fuel being delivered, such as a clogged fuel pump or even due to a clogged fuel filter. I think it is worth keeping in mind that not only the static pressure of the fuel pump system needs to be tested in this case, but its dynamic operation.
I would like to note that this situation - so the lean air-fuel mixture - can also happen even if the engine sucks false air from somewhere - often due to the wrongly mounted throttle body seal -
or even the defective MAF or MAP sensors can cause such a failure symptom too.
In this case, the fuel consumption will be too low, and it will be difficult to start the engine, and may even stop easily. In addition to this - which is especially harmful in such a situation - the valves together with the pistons will heat up and wear much better because the necessary amount of injected petrol - if not a direct injection engine - would also cool and lubricate the valves and the engine.
Anyway, the small amount of fuel in the mixture is even visible on the electrodes of the bleached spark plugs. Of course, the most important thing is that the composition of the air-fuel mixture should be always around lambda 1.

Inspection of the Zirconium dioxide O2 sensor
The O2 sensor can store - directly or indirectly - even multiple DTCs in the PCM memory, which will - almost without exception - switch on the yellow Check Engine MIL lamp too. Anyway, the lambda sensors are designed for a mileage of around 200,000 kilometers, which is quite a lot. So in the case of an oxygen sensor DTC, it is not at all certain that the sensor itself is defective. There can be a lot of reasons for this, such as a bad or dirty mass airflow sensor, or an incorrectly adjusted engine control, or even a clogged fuel pump or even a bad ignition system, and so on. It's worth keeping in mind that the excessive oil consumption of the engine significantly reduces the lifetime of the oxygen sensor.
In case of a quick inspection of the oxygen sensor, the resistance of the heating wires can also be measured by a simple multimeter even at home too, which should be only a few Ohms in a cold state. Furthermore, an oscilloscope will be needed for more serious examinations, which is also not very complicated, because, during operation, this heater unit has to give a pulse width modulated (PWM) square signal according to its temperature, so that the warmer the lambda sensor, the smaller the fill factor of the square signal, since a nicely heated sensor requires only less energy to keep its temperature above 300 ° C.

55

68

104

55
1/9
Regarding the output voltage signal of a fault-free oxygen sensor can be said basically that the correct voltage signal sent to the PCM controller must change dynamically between 0 and 1 V depending on the engine speed, and if this signal is constant during operation, something is wrong with the lambda sensor.
I think it is very easy to keep in mind that the output voltage signal of the zirconium oxide type lambda sensor can vary between 0 and 1000 mV. Moreover, if an output voltage of about 100 to 200 mV can only be measured on the signal line of the oxygen sensor, this simply means that the engine is running with a lean fuel mixture at that moment, and in the case of a rich fuel mixture, the lambda sensor will produce output voltage values ​​between 500 and 1000 mV. After all this, I think so it is really very easy to understand that when the PCM controller continuously adjusts too rich air-fuel mixture for the engine, then the Lambda sensor can only produce output values ​​between 500 and 1000 mV even when the engine is hot. I think it is easy to imagine that in the other case when the PCM controller continuously sets a lean fuel mixture for the engine, then the Lambda sensor can only produce output values ​​between 100 and 400 mV even when the engine is hot. So in short, it is easy to see that the higher the actual voltage value, the richer fuel mixture will be set by the PCM controller.
Let's not forget either that the response time of an old lambda sensor increases significantly over time, and basically it is also very true that the better the quality of a lambda sensor, the faster it can respond to the changes.

If the Powertrain Control Module does not receive any signal from the defective lambda sensor, then the PCM will handle that situation as a continuous engine cold start, and it will set a rich fuel mixture for the engine. By the way, I think so, if the sensor needs to be replaced, then it is advisable to unscrew the faulty lambda sensor when the exhaust manifold is still warm but not too hot, as the sensor and its environment can be very corroded.
Of course, not all vehicles have a lambda sensor since the exhaust system of older intake diesel and turbo diesel engines - still equipped with diesel fuel dispenser unit - does not have a lambda sensor either, and in addition to this, there is no throttle valve or MAF sensor neither to control and monitor the intake air volume because the amount of intake air is always maximum in these constructions, and the diesel fuel dispenser unit regulates electronically the amount of dispensed fuel based on the cylinder capacity, engine speed, intake air temperature, diesel fuel dispenser nozzle sensor and so on parameters.
Thank You for reading this article!
bottom of page