top of page
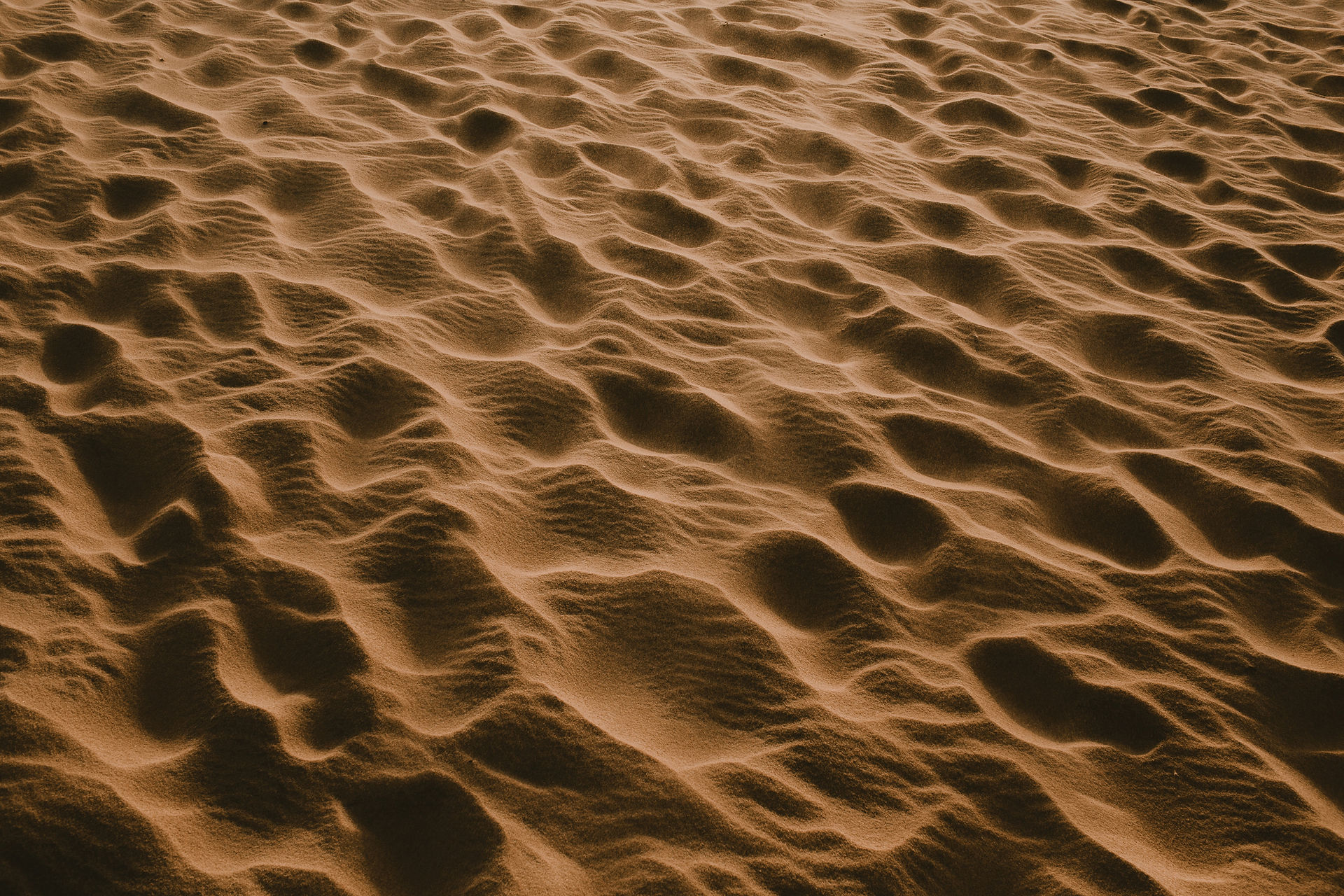
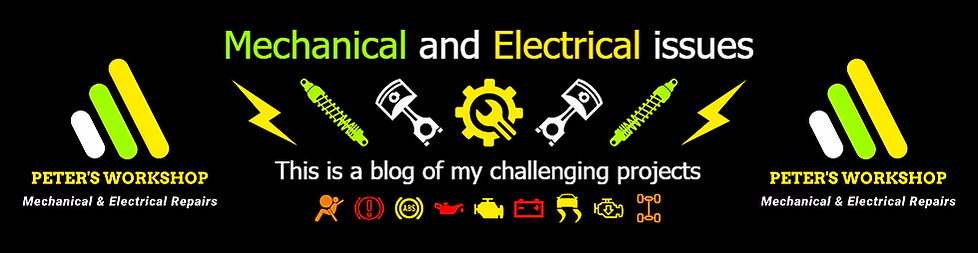
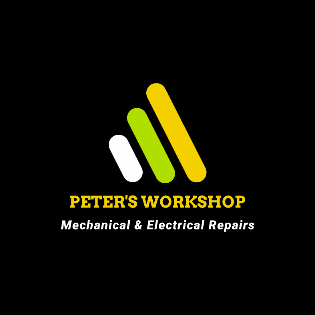
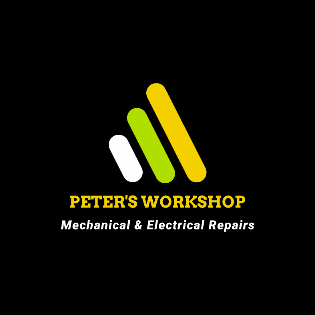
OPINIONS AND THOUGHTS
Lead Acid Batteries
Complexity: Medium
The very first Thoughts
​
In my opinion, lead-acid batteries can never be completely eliminated from the market. I'm sure everyone guesses that the subject of batteries, in general, is quite a complex and tremendously huge area.
I'm writing this short summary to help You to navigate in the complicated world of lead-acid batteries. So in this article, I would share a few thoughts I have collected over the years, but within this beautiful topic, I will focus primarily on the lead-acid starter batteries.
I try to formulate these few lines in the simplest way. So they can be understood hopefully without any particular knowledge.
I would like to mention here that I also designed and built various devices for the maintenance and testing of lead-acid batteries, but after I have consulted with design engineers and experts I felt more and more that this area is not as simple as I first thought 10-12 years ago. It is an especially serious profession to which could You dedicate quite easily a few decades of work.
I'm also sure that not many people can really say they know absolutely everything about all kinds of batteries. I would like to emphasize here that this is not a doctoral dissertation and I only deal with lead-acid batteries as a simple hobby. I wouldn’t be surprised if a sentence or two needs to be adjusted. So I would be very happy to receive corrective feedback too. Let's start at the very beginning where most people may have problems with notations and meanings too.

Grouping Batteries from different Aspects
​
Lead-acid batteries can be classified into 3 major groups for average users such as cyclic operation mode batteries, starter accumulators for vehicles and there is a third group that combines the features of both types, these are called as dual-purpose accumulators. Usually many do not even know the previous grouping neither, but for experts, slightly more sophisticated groupings are possible which could be the following:
Regarding the cell designs, the batteries can be basically:
- non-sealed or open liquid electrolyte type lead–acid,
- sealed and valve-regulated with bounded electrolyte type lead–acid, so VRLA like AGM,
- and last but not least the also sealed but completely closed structure lead-acid.
So that the first abbreviations have come up, let’s move on its meaning quickly:
- VRLA: Valve Regulated Lead Acid
- AGM: Absorbed Glass Mat
- SLA: Sealed Lead Acid
- MF: Maintenance-Free
​
The alloying materials fall into another classification, which is already a bit more complicated for everyone and most of the additives are known for the average users neither. This is a very complex topic not to mention the issue of recycled lead.
So for conventional accumulators mostly antimony (Sb), silver (Ag), and calcium (Ca) alloy materials are used in different mixtures and proportions, but to make the story more complete, lead-acid batteries could contain in addition various tin (Sn), zinc (Zn), selenium (Se) and carbon (C) additives too, which could mean benefits not only for manufacturing processes but for battery performance too, such as cycle time or higher discharge current or high effectivity against sulfate formation, etc.
In the following sections, let’s just focus on the lead-acid starter and cyclic operation mode batteries.

Cyclic operation mode lead-acid Batteries
​
My first group includes the cyclic operation mode batteries, like traction and various buffer batteries. Their main feature is that after charging I can discharge them slowly without any damage. So the cyclic operation mode means the alternation of continuous charge-discharge states. Compared to starter batteries, the cyclic batteries have longer periods with a greater current load than charging current, but they don’t like so much when they are shocked suddenly with as much current as starter batteries.
These types of accumulators fall mostly into the non-maintenance free category. In other words, we need to pour water into the cells more often and take more care of the charging current as well. These batteries are used to drive mainly electric motors, such as in a simple forklift, or for example, in the case of island solar systems only cyclic batteries can be taken into account for both charging types (MPPT or PWM) as well.
As far as physical and electrochemical characteristics are concerned most of the cyclic lead-acid batteries typically contain mainly antimony additives instead of calcium and such auxiliary alloys that support the higher current release over a longer period of time. As for the internal structure, the lead plates of cyclic batteries are usually thicker than in starter batteries because these batteries are not sharpened to the small internal resistance. For all these reasons, the cyclic batteries are much more tolerant with deep discharge loads, however, starter batteries don’t really like these situations. Due to their composition and structure, the harmful sulphate formation is also a serious problem in the event of a longer shutdown.
It is important to note here that the charging signal of cyclic batteries is basically the same as starting batteries of-course only in the conventional lead-acid category. Don't forget that lead-acid chargers should not be used for gel batteries at all.
However, their application fields are completely different, I know that due to ignorance, many people use simple starter batteries in cyclic operation mode.
The side image shows the electrolyte level inspection. The electrolyte is clear transparent and the level indicator indicates the proper sulfuric acid level.
However, a cyclic battery is shown in the picture below it is a closed MF (maintenance-free) type.

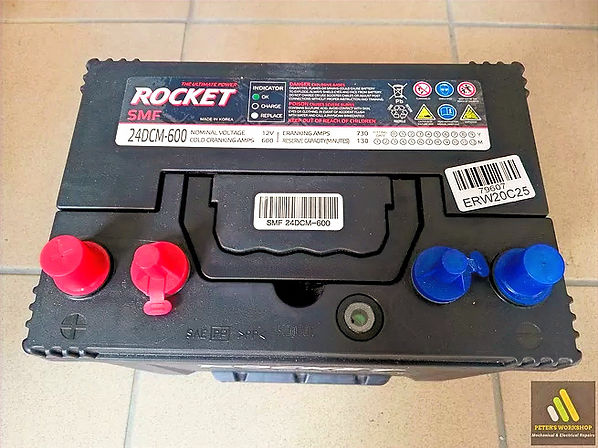
Lead-acid starter Accumulators
​
One of the main purposes of starter batteries is to supply current to all electrical consumers in the vehicle when the engine is not running. After starting the engine, the generator takes over the main electrical tasks and continuously charges the battery too.
In addition, the starting accumulator must store enough energy to keep the engine running for enough time to be serviced within 50 to 100 km, when the generator or the voltage regulator is not operating. This is called as reserve capacity, which is a requirement for starter batteries and has also been defined by car manufacturers.
That was already clear to me from my previous measurements, that lead-acid starter batteries can tolerate the sudden current push very well compared to other batteries. It is almost unbelievable that this electrochemical storage device is capable of delivering up to hundreds of Amperes to the starter motor as the largest electric consumer of a vehicle, after that it is able to process a sudden - 30-40 Ampere - current push from the direction of the generator and they can reproduce this task up to a thousand times.
I think this is quite surprising to everyone, especially at first hearing, but there is a nice example of this interesting feature a little below. If we think about it further, the main condition for the high current flow is usually the smallest possible resistance.
This is easy for everyone to understand because the current always likes to flow in the direction of the lowest resistance. Let's just think about insulating materials since the high resistance is not liked by electric current. Moreover, if we want to transfer a large current through an electrical conductor, it is worth doing it with the smallest possible resistance.
So that would be the best for a good starter battery if its internal resistance is as low as possible. These above-mentioned rows make it easy to understand that starter batteries have thinner lead grids than in cyclic batteries because the thinner the lead plates the lower the internal resistance.
Giving lifelike examples, I made some measurements with lead-acid starter batteries.
The picture below shows the cranking and charging voltage of a battery (12V, 52Ah/520EN) which belongs to a Ford Fusion 1.4 Duratec engine.
It is nice to see that the voltage dropped to 11V only for a very short moment when the engine was started. It can also be read from the graph that the voltage of the charged battery drops back slowly when the engine was stopped after 2 minutes.

Everyone knows that the starter batteries cannot be discharged below a certain critical voltage level. This type does not like the long-lasting loads so much, however, these batteries can be shocked multiple times by hundreds of Amps in case of ignition periods and this is the biggest difference compared to the cyclic batteries. So again the lead-acid starter accumulators are very good if an electric consumer, like a starter motor, wants to take out a huge amount of current for a short period of time and then the generator charges it back very quickly as shown in the picture below.
It can be read from the graph that the starting current jumps to a value around 108 A, then after starting the generator it suddenly pushes the battery by 38 A, so the battery is not pampered by the generator in the car.
From all of these can be concluded that the starter motor delivered about 1200 W at the moment of start-up, which was powered by the lead-acid battery.

After this brief overview let’s take a short look at the internal structure of lead-acid batteries.
What is inside the lead-acid Battery?
​
First of all, I’d like to share some useful tips and experiences at the very beginning.
It is known that sulfuric acid is a strongly harmful, toxic, and extremely caustic material.
Moreover aggressive liquid has already splashed into my eyes because I didn't wear protective glasses, and I was once in the emergency department for a similar reason too.
Therefore, I would recommend that when the acid drains out from the battery you should have safety glass and protective gloves to protect yourself, and in case of acid leakage you need a little baking soda to neutralize the acid.
The acid content of the electrolyte can also evaporate, but mainly due to chemical reactions, its water content evaporates faster. So I hope everyone knows the sulfuric acid is never poured into a battery to adjust the liquid level. Furthermore, the lead is also very toxic, therefore always use gloves before cleaning the terminals and so on.
Let’s get back to the technical content.
​
As I indicated in the picture above, after removing the caps you can take a short look inside the battery and check the acid levels. So there are 6 individual cells and each cell generates about 2 V and if you add them up you will get 12 V.
It is well-known that on the top of the battery there are positive and negative terminals and it depends on the location and type of the lead plates which pole goes where exactly. This way the circuit inside is very simple because each individual plates are connected to the positive or negative lead rail. In this sense, there are negative lead plates and positive lead-dioxide plates, and simple lead conductors go across the cells. So in summary each set of lead plates are connected to the negative pole and each set of lead-dioxide plates are connected to the positive pole.

The lead plates are basically different types of simple lead grids such as mesh-structured or more recently expanded which can give the surfaces for both types of microporous mass.
The porous lead and lead-dioxide mass are essentially intended to increase the reagent surface area because in this way the sulfuric acid nicely fills the pores of the spongy positive and negative electrodes.
Each cell containing 8 rolled plates inside in the following way. Usually, four of the lead plate grids are negatively charged and are coated in a gray microporous lead paste, and the other four are positively charged and these are also coated but with brown microporous lead-oxide mass.
The plates are crossed with each other, although they are separated usually by plastic-based bags and/or fiberglass blankets, which depend on the battery type.
In the pictures below you can see how the surface of the negative and positive electrodes looks like.

The picture below clearly shows the characteristic brown color of lead-dioxide on the positive lead plate grid.

As regards the standard cell structure there is a positive stack of brown lead-dioxide plates, pocketed one by one in bags which could have more additional chemical protective layers as well and there is a negative gray lead plate stack wich could have also a microporous separator layer. The positive and negative stacks are slid into each other one by one and the plates are connected to each other in both stacks by a cast lead rail, and that way they are placed in the separate cell container as shown in the picture below.
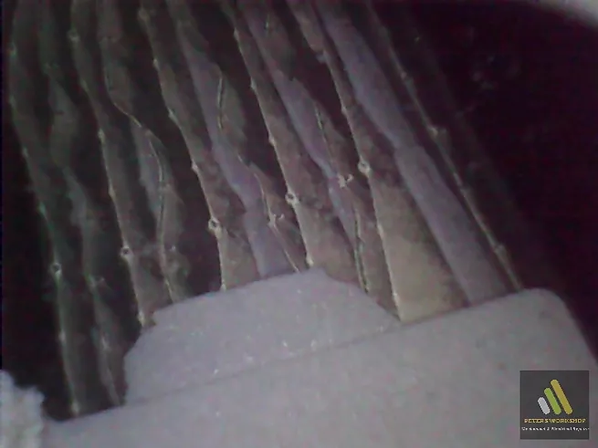
What is the main role of the plastic-based separator bags?
​
With the help of the (polypropylene or polyethylene) separator bags, the side short-circuiting of lead plates and the short-circuiting due to active mass loss can be prevented. I was also thinking about how the polypropylene separator might come into play in this question because it is an insulating material from an electrical point of view and in addition, it should be completely permeable to sulfuric acid, but yes we are talking about highly microporous materials which are fully permeable to the electrolyte.
Thanks to the thin separator bags the plates can be placed much closer together and there will be no short circuit either. This way the volume of the batteries could be reduced because there is no need for a sludge collection space on the bottom of the battery. Thus, even larger plates can be used too, as they can extend all the way to the bottom of the plastic container.
So in other words the separator bags are permeable plastic-based membranes that form basically a microporous layer around the grids. Depending on the technology they exist in many different designs and variations. I recently heard that there are batteries, whose negative plates are coated with carbon-containing chemical layer too. The carbon additives on the negative plates have among others that very advantageous property that can very effectively inhibit the sulfate formation of lead grids.
The polypropylene separator bags are clearly visible inside this damaged and already acid-free battery shown in the picture below. I would like to draw Your attention to the thick sulfate layer, which is a rigid salt formation on the plates and it is very difficult to break that with electricity. In addition, the regeneration process takes a very long time because the sulfate layer insulates the plate surface from the electrolyte.
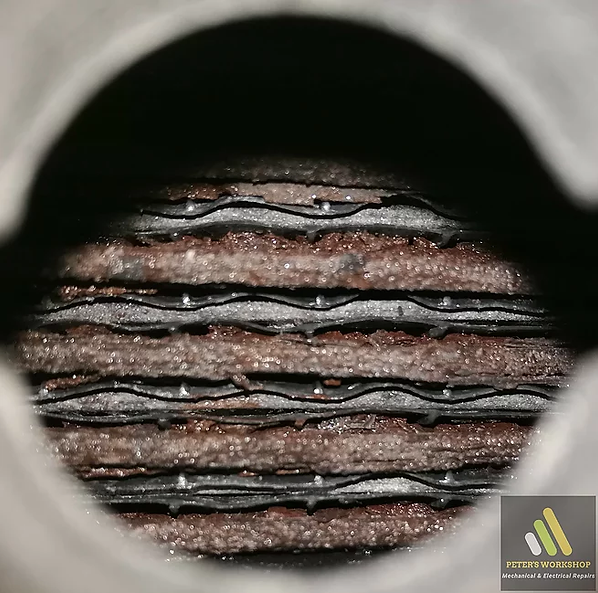
I think it's important to mention here that fiberglass blanket separators are used in most batteries of motorcycles and off-road vehicles where the total electrolyte content is soaked by fiberglass blanket.
So these are the so-called AGM - absorbent glass mat - batteries as shown in the image below. The internal resistance of these accumulators is very low therefore they have a very high starting current.
​Most people mistakenly call these as gel batteries, but the electrolyte of the gel battery has a completely different structure because, in the gel battery, the electrolyte is gelled using silica gel. Furthermore not to mention that the lead-acid battery charger cannot be used for the gel battery.
The white material shown in the side picture is called a fiberglass blanket.


Reversible chemical Reaction?
​
Yes, because accumulators can give and receive electricity.
The electrolyte contains about 25-30% sulfuric acid and as I said the lead plate grids are connected to the negative anode and the lead-dioxide plates are connected to the positive cathode.
In case of load, both are converted to lead sulfate:
​
Pb + PbO2 + 2H2SO4 <=> 2PbSO4 + 2H2O (+ 2e-)
lead + lead-dioxide + sulfuric acid <=> lead sulfate + water (+ electrons)
So during my high school years, I had already learned from chemistry lessons that this formula explains to us briefly when the battery is discharged, the electrolyte continuously loses its sulfuric acid content. As a result of this, a crystallized primary lead sulfate salt layer is generated on the surface of the lead grids, which is easily dissolvable in sulfuric acid.
Meanwhile this process some water is generated and further 2 electrons are released which can finally ensure the flow of the electric charge. The generated water will be mixed as a liquid in the electrolyte by the diffusion effect and as a result of this, the sulfuric acid density will decrease in the electrolyte.
When we are charging the battery, this process is, of course, reversed.
Due to the influence of electric charge, the mentioned crystallized primary lead sulfate salt layer on the surface of the lead grids will dissolve back into the electrolyte as sulfuric acid again
but the distilled water content will simply evaporate and as a result of this, the density of the electrolyte will increase.
This is the reason why need to be refilled the battery cells only with distilled water from time to time. Don't forget that we never pour sulfuric acid into the cells because the sulfuric acid cannot evaporate so much. On the other hand, the sulfuric acid content of more than 30% would corrode the lead grids and destroy the battery.
Anyway, the lead-acid batteries have an average lifespan of about 500-1000 charge cycles and the energy density of these is pretty low 30-50Wh/kg and I remember hundreds of Wh/kg for other types of newer and non-lead-acid batteries.
If I’m already talking about the electrochemical reaction, let me note that the water decomposition process begins if the charging voltage per cell exceeds the critic 2.39 V which means a value of around 14.4 V in charging voltage. Anyway, the water decomposition can cause an explosive gas generation as well.
However, it's also true that some suitable catalyst has been used in the case of lead-acid batteries to convert this explosive gas mixture back into water which helps to prevent the excessive gas generation with good efficiency, but this problem did not go away completely.
To the best of my knowledge, with the appropriate ratio of lead to tin and calcium alloy metals, there should not be water decomposition independently of the age of the battery below the 14.4V charging voltage.
This could be one of the reasons why calcium-containing batteries have a much longer lifespan.
Moreover with completely pure Ca technology the battery can be completely enclosed without any valves. In other words, the battery does not need to be refilled with liquid during its life.
The charging voltage signal approaches the water decomposition limit in the picture below.

Evolution of lead-acid Batteries
​
Briefly, in the same plastic container size, the internal resistance of batteries is reduced and their cold-start current is significantly increased.
In the good old days, there were still plain cast lead-plate batteries with thick bituminous and hard rubber walls with traditional lead rail top connections. In these energy storage devices, the thickness of the cast lead plate was typically around 2.5-3 mm, which is quite thick compared to the nowadays used 0.7-8 mm.
It is a well-known fact that after separator bags were placed on the market, the conventional batteries could gain many advantageous properties. This development has increased the number of lead plate grids that can be placed in the same cell volume. The lead plate grids became about 3-4 times thinner and the grid construction also changed several times.
​
In order to further increase efficiency, the location of the grid poles has continuously changed with the help of deeper optimization calculations, because in the case of starter batteries, a small decrease in resistance already means a lot during the delivery of a huge starting current.
So the internal resistance was further reduced thanks in part to these changes and due to the thinner polypropylene walls. Moreover, the surface of ​​the lead plates increased in the same plastic container volume which meant more acid as well. In summary, we can say that the capacity of the lead-acid batteries has sharply increased over the years.
Anyway in terms of the newest marketing and technical development the current "peak type" is the spiral cell high-performance starter battery. This type, despite its small size, is capable of delivering an extremely high starting current. Moreover, its reserve storage capacity is about 30% higher than the conventional lead plate batteries. In addition, it contains a bound electrolyte and even in case of damage, it is able to work for months.
By the way, they are not very complicated from a structure point of view, because in these accumulators you can find large cross-section cast cell bridges from high purity lead and rolled high purity lead electrodes with a large active surface and as I mentioned the electrolyte is impregnated in microporous fiberglass separator blanket.
What was the greatest Development?
​
As far as lead plate grids are concerned, on the next development levels not only the plain cast lead plates were used as in ancient times. So during newer manufacturing processes, different types of soft lead masses - mixed with appropriate alloy materials - were rolled into the grid surface as an electrochemically much more active reagent layer.
The problem was that depending on the quality and usage of the battery, smaller or larger pieces of this relatively soft active mass layer slowly exited the grid surface during usage and aging.

This kind of corrosion process is due to direct contact with sulfuric acid and partly caused by mechanical resonance and thermal loads as well. As a result of this fact floating lead particles in the electrolyte can form an electrically conductive deposited sludge layer on any surface.
On the one hand, the mentioned separator bags were used to collect this floating sludge for several years. Thus, the chance of a cell short circuit is significantly reduced.
As I mentioned at the beginning recently, in addition to these separator bags, different chemical protective layers have also been applied to protect the surface of the active mass. So the most important goal was to prevent the active layer from leaving the grid surface. The side image shows a very old sulfate crystallized and fragmented lead-acid battery.

What about the self-discharge Process?
​
The batteries slowly lose their charge, even if they are only stored in the workshop without any external consumer. This is a completely normal process, but its speed depends mostly on the age and ambient temperature and last but not least on the quality of the battery as well.
To reduce the rate of self-discharge, different additional alloys - mostly Ca - are used in the lead grids to increase the mechanical strength of the soft active mass.
Furthermore, the high purity lead cannot generate corrosive crystal elements which are energy-consuming areas on the grid surfaces and they are mostly the responsible for self-discharge.
So the purity of used lead plates is also a serious factor in quality issues, but the lead cleaning process is very expensive.
Of course, the self-discharge rate of a premium high purity lead-acid batteries should be much lower because these batteries can be parked for about a year and a half without charging.
PbSb antimony alloy batteries
​
In the technical language, the combination of the lead-antimony alloy is called as "hard lead", therefore it is no surprise that lead is combined with antimony (Sb) for the reason of higher resonance tolerance and better pourability features for production. So as a result of this, much harder lead grids can be produced as if only pure soft lead cast plates would be used by factories.
Manufacturers do not publish much about alloys or internal resistance either, but I think that's for sure in the case of cyclic operation mode lead-acid batteries, the antimony is the main alloying material instead of calcium. The main reason for this is the need for frequent maintenance.
It's also true, that I only see the calcium content on most labels of non-sealed batteries, but in spite of this fact, it can be surely said that the conventional 6-cap batteries are mainly antimony-containing types and I quickly note that they can also contain some calcium additives as well.
I will also explain why I think so.
In my opinion, cheaper batteries may have higher antimony content because the cleaning process of recycled lead is very expensive. Furthermore, I have heard and read several times that most of the alloys cannot be removed so easily from the molten recycled lead mass.
So it follows for me that there are still antimony alloys in the plates of recycled batteries and they won't wear out until tomorrow due to the endless and continuous recycling process.
It is known that the self-discharge rate of conventional antimony alloy (PbSb) batteries is much higher than the self-discharge rate of calcium alloys (PbCa) batteries and surely many electrical experts have already met with the main disadvantage of antimony alloy batteries. It comes from that reason the antimony can slightly corrode the negative lead plates, which blocks the lead particles in the porous lead mass to take part in the electrochemical processes. Thus during charging, the absorbed electric current begins to decompose the water.
​Unfortunately, this process is getting faster over time. If the antimony alloy battery is still young, which means less than a year, then this problem is not experienced as much.
Therefore I know that why are older vehicles more compatible with traditional antimony alloy batteries than the newer ones. The reason for this is that in older vehicles the charging voltage of the voltage regulator is around 13.8 V and not 14.4 V as in the newer one.
In other words, if we put an antimony alloy battery in newer cars, it would speed up the water decomposition when the battery is aging due to the higher 14.4V charging voltage.

It is well known that a generator is an electrical machine that converts mechanical energy into electrical power. The voltage generated by the alternator is set by the voltage regulator to a constant 14.4 V in most vehicles. In other words, the charging voltage is always constant at 14.4V in all cases, i.e. it cannot be adjusted and exactly this is the most important point from the water decomposition point of view.
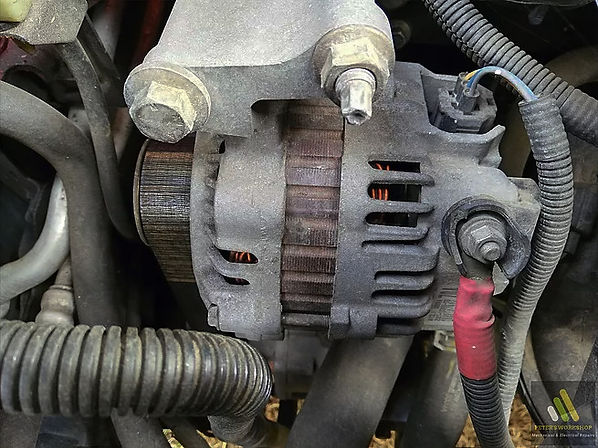
PbCa calcium-alloy batteries
​
The calcium has also a similar beneficial effect on the durability and pourability of lead plate grids during production and against the mechanical resonance. Moreover, the Ca content can not cause as high corrosion as antimony on the negative lead plates because it's more stable from an electrochemical point of view, but of course, the battery is not eternal with the Ca technology either.
Don't forget that there are completely pure calcium batteries, but not all calcium accumulators are completely antimony free. I know from experts and mechanics that most calcium batteries are manufactured with low antimony content positive grid and calcium content negative grid.
As I said the calcium-alloy batteries like much better the constant 14.4V charging voltage in long term than the traditional antimony batteries and these accumulators can be stored for up to a year without charging in the workshop because they are not really affected by aging so much.
I think the more sophisticated vehicle owners have already experienced that non-sealed (antimony alloy) batteries have a higher self-discharge rate than completely closed (calcium-alloy) batteries. Moreover, new cars are usually equipped mainly with high purity calcium-alloy batteries which can last for up to 8-10 years.
What may be mentioned as a disadvantage is perhaps that the calcium-alloy batteries can not tolerate the deep discharge phases and overvoltage situations so much, but in my experience, they are not damaged drastically easily because of these either.
The mentioned water decomposition should not happen in case of calcium alloy batteries below 14.4 V charging voltage so these energy storage devices can be completely enclosed.
Therefore most of the sealed Ca batteries have a porous plug at the central gas outlet or a simple membrane breathing valve due to the generated vapors and gases. Moreover, its plastic cover is equipped usually with a safety valve too for that reason if the charger fails.
It is important to note that above the 14.4 V charging voltage the water decomposition will start here as well. Anyway, it can’t happen so easily nowadays because the electronic control units are continuously monitoring the overvoltage situations with multiple feedback. These are the reason why could be the Ca content good marketing information for any batteries.
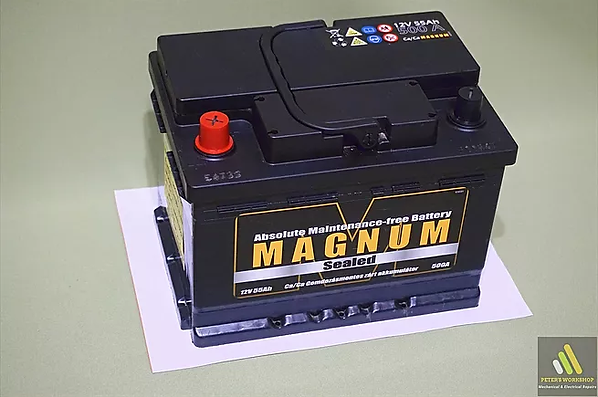
Thank You for reading this article!
bottom of page