top of page
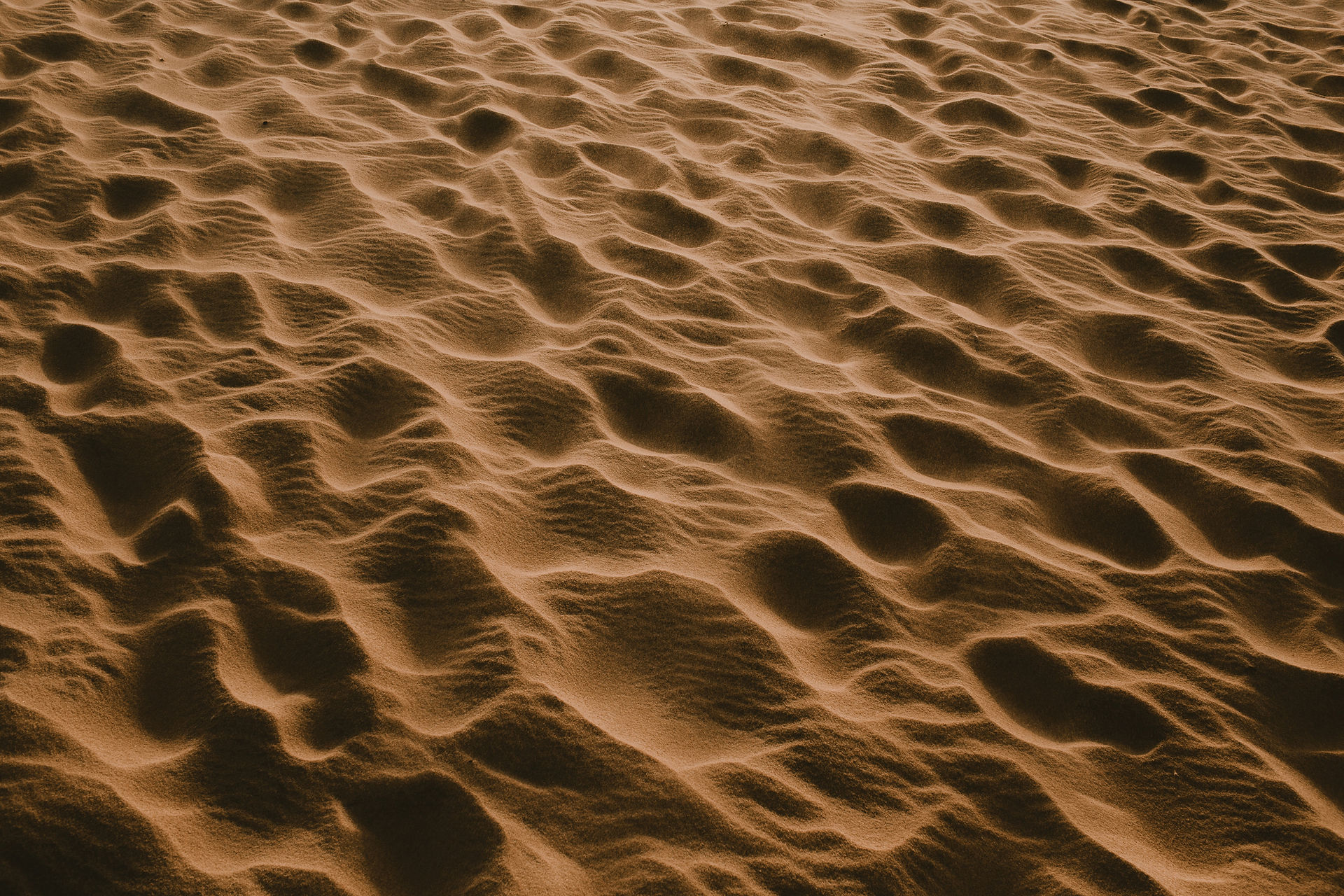
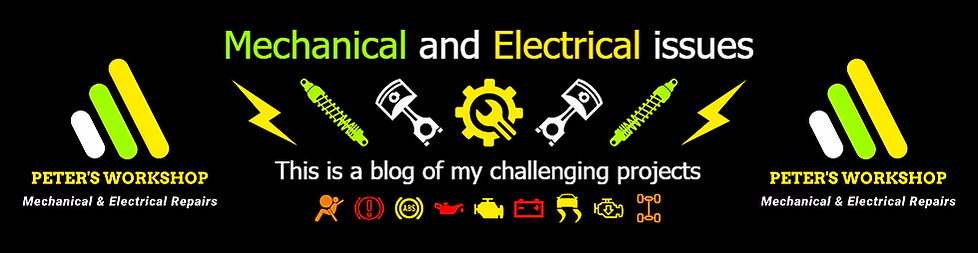
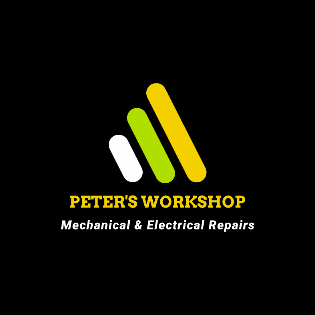
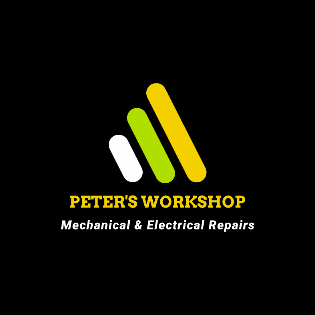
ELECTRICAL
Drilling Station Renovation
Complexity: Medium
Industrial Drill Renovation
I decided to write a few sentences about this enjoyable challenge because this project may even encourage colleagues like me to preserve similar technical values ​​for the future. I have had many types of drilling machines before, but high-precision holes can only be made with a much more serious drilling station. Not to mention the cases where holes with a larger cross-section - such as 20 mm - need to be drilled out in a more serious hardened steel profile.
There is no question that an excellent drilling station made of sufficiently robust and high-quality materials can very quickly be one of the most beautiful pearls in the workshop. I illustrated in the image below my high-speed steel drills that - as can be seen quite clearly from the dimensions - already require a higher level of metalworking infrastructure.
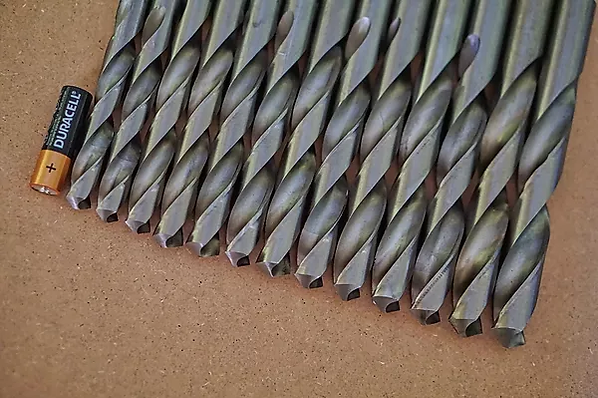
I was looking for a brand new drilling station for a long time, and I checked the offerings of stores, but unfortunately, I couldn't make a meaningful choice. The best solution was a used drilling station from an industrial metalworking company, which was already a more acceptable machine for me.
The most important factors were that its frame structure is quite robust so it weighs about 100 kg, its bearings are excellent and easy to replace, and finally, it is powered by a 3-phase star/delta electric motor. With its special capabilities and high torque, it is an important tool in industrial series production, but I will only use it for occasional high-intensity tasks.
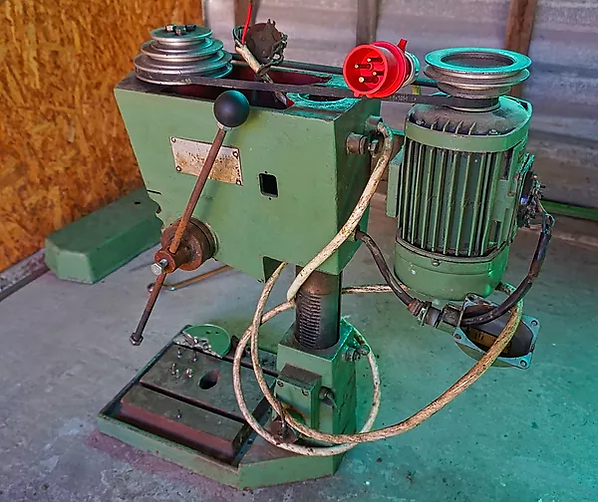
Of course, it originally operated from a 3-phase AC 400 V input, but I decided to convert it to a 1-phase AC 230 V, which is one of my favorite tasks anyway. The copper windings of the three-phase motor were in excellent condition, however, the complete electrical wirings and switches needed to be replaced.
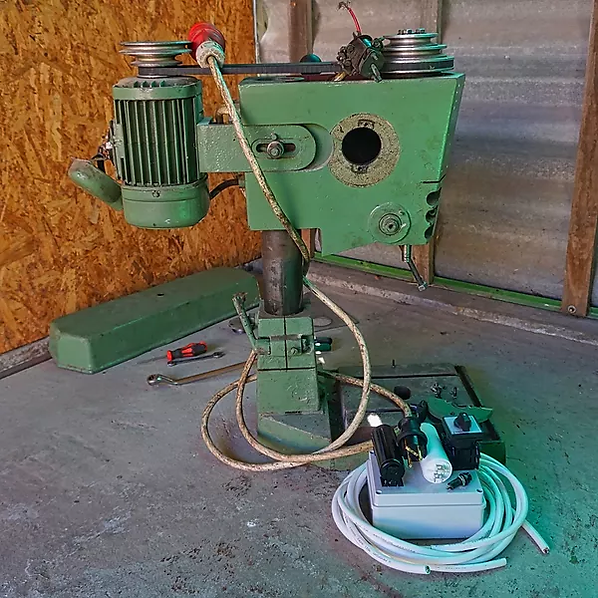
In my electric motor, the DELTA terminal box connection had to be used for the AC 230V single-phase supply. I also made a detailed summary of this in the figure below, which was a solution only and exclusively for my own case.
Of course, if you do not have an appropriate qualification in the field of electronics, always call a specialist! Before I move on, I would like to emphasize that it is strictly forbidden to carry out any electrical installation or reparation without confident knowledge and proper qualification!
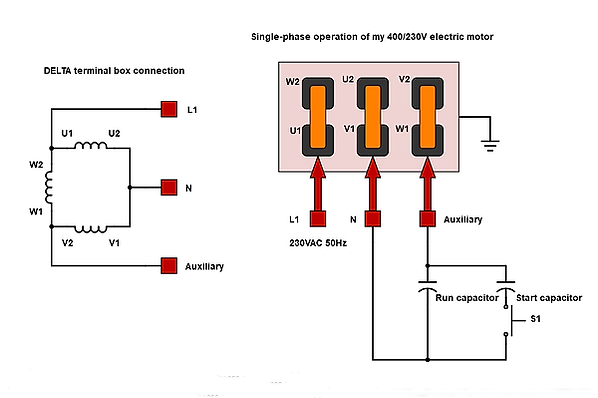
I designed properly sized run and start capacitors into my circuit for a more balanced operation and proper starting abilities.

I refined the operation of the electric motor by setting the voltage of the auxiliary winding to around the ideal 220V.
After all this, I performed load tests on the electric motor to check its operation under dynamic conditions.
The AC 230V single-phase supply is a kind of forced operation for 230/400 V delta/star electric motors, but after a small correction of the constant operating capacitor, I was satisfied with the results of my measurements.
Of course, for a similar purpose, a single-phase frequency converter would be the perfect solution with a 3x230V 3-phase output, but that's enough for me now.

For more comfortable and efficient work, high-brightness LED work light has been added to the drilling station.
I believe that such renovation processes should always be carried out systematically and patiently to achieve the desired result.
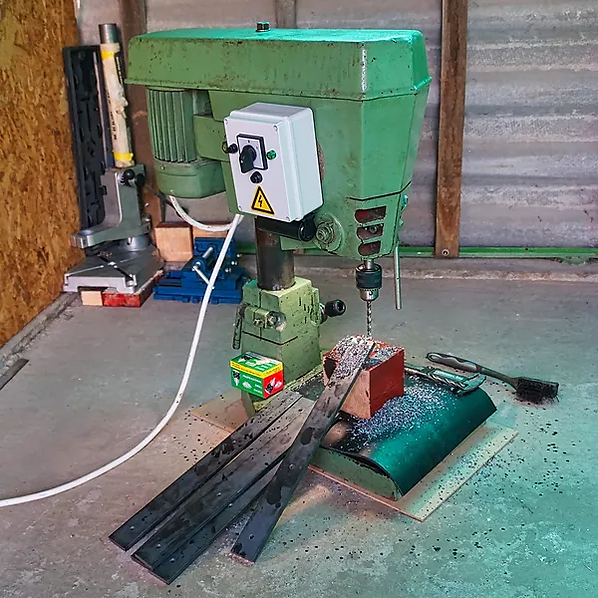
I also ordered a much more robust drill chuck that would already be suitable for industrial use.

Thank You for reading this article.
bottom of page